The annealing process used to alter the physical properties of a material, it involves heating the material to a specific temperature, maintaining that temperature for a certain period, and then cooling it down. This process can relieve stress, increase ductility, and soften the material, making it more workable. Heating the material above the critical temperature, followed by slow cooling. This results in a uniform microstructure, typically used to soften the material.
Industries Served:

Agriculture Industry

Auto components Industry

Aluminium Industry

Aerospace Industry
Material Grades That Can Undergo The
Annealing
Material
Tool Steel, Carbon Steel, Alloy Steel, Non-ferrous Alloys, Super Alloys, Stainless Steels
Material Grade
AISI D2, O1, H13, H11, M2, T1, AISI 1010, 1020, 1040, 1050, 1080, 1095, AISI 4140, 4340, 8620, 9310, C11000 copper, Inconel 718, Monel 400, Inconel 625, Hastelloy X, Stellite 6B, AISI 304, 316, 430, 446, 410, 420
Annealing Furnaces
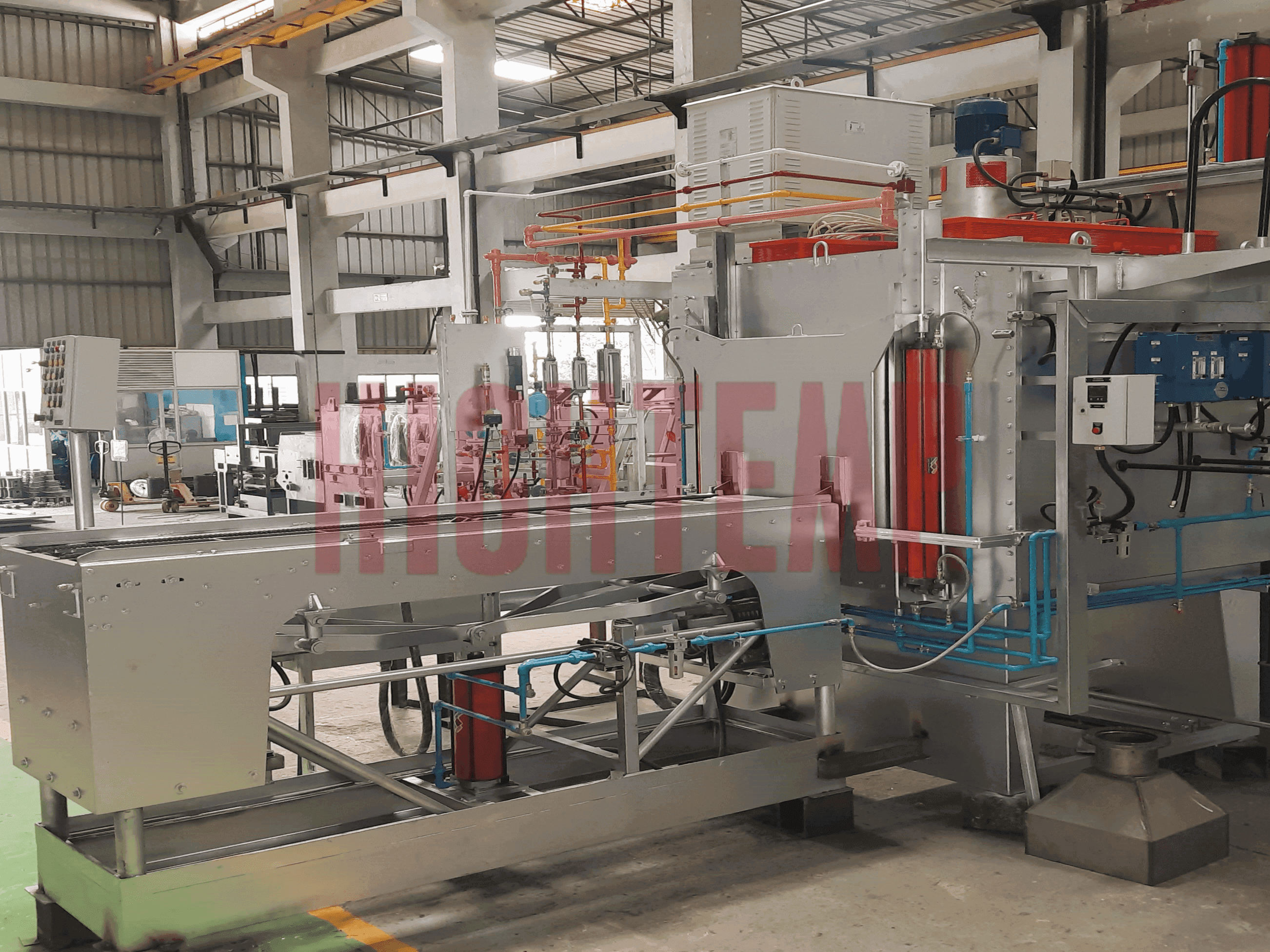
Integral Batch Sealed Quench Furnace
Sealed Quench Furnace (SQF) is used for high-precision heat treatment primarily in auto components industry. This allows heat treatment for carbon steel to reach the desired hardness and strength. The furnace feature allows the materials to be processed in batches rather than continuous operation. HIGHTEMP is the leading manufacturer of Sealed Quench Furnace in India that provides a global clientele, with sales volume exceeding 500+.

Chamber Furnace
HIGHTEMP's Chamber Furnace is a reliable solution for batch heat treatment, offering excellent temperature uniformity and precise control. Its robust design ensures durability and consistent performance, making it suitable for various applications. The furnace is engineered for efficiency, delivering high-quality results with optimal energy usage.
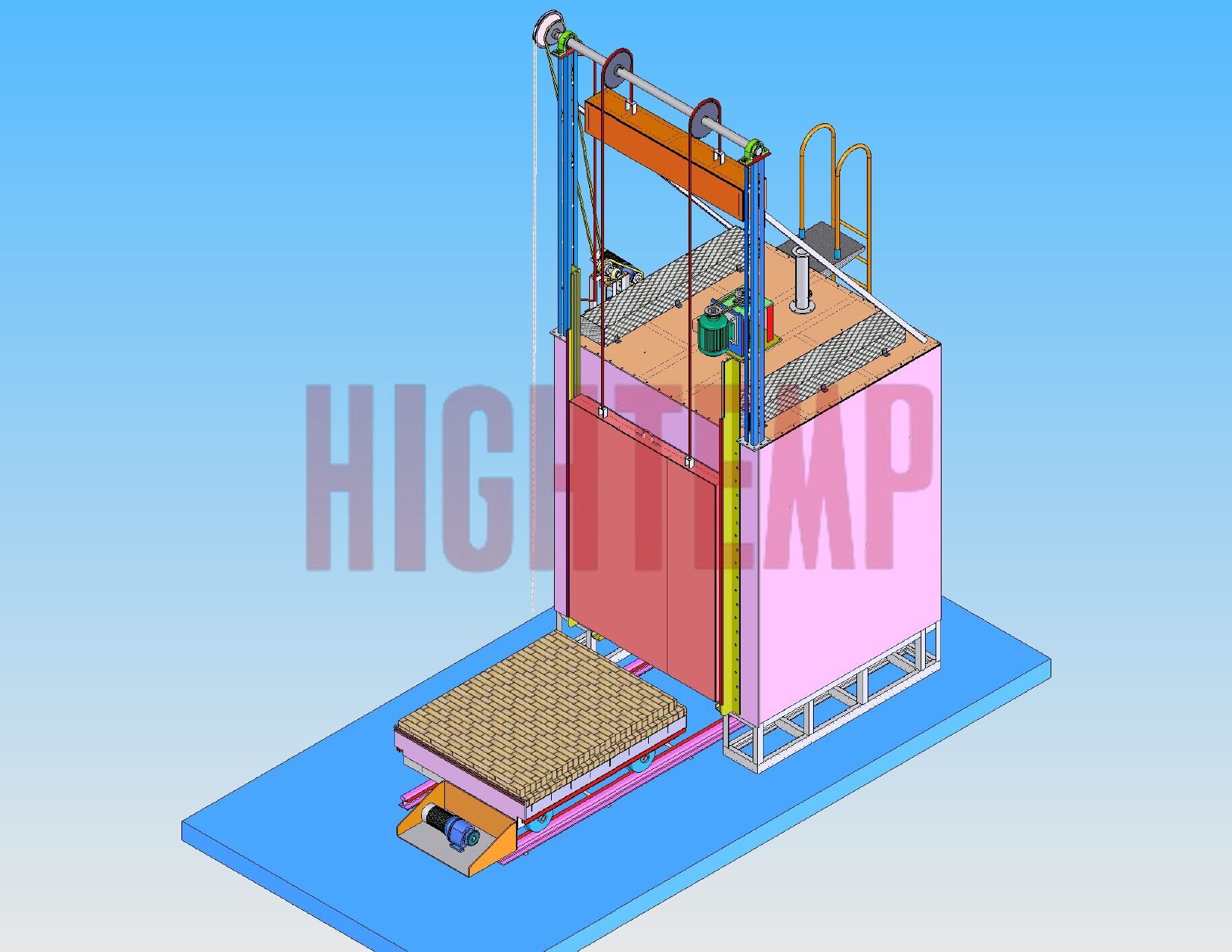
Bogie Hearth Furnace
HIGHTEMP's Bogie Hearth Furnace is designed for the heat treatment of heavy and large components. Equipped with a bogie, the furnace simplifies the loading and unloading process, making it ideal for applications requiring precision and uniform heating. The insulation and efficient heating systems ensure energy savings while maintaining superior performance. This furnaces can be customized with single or double doors and single or double bogies to meet specific user requirements. Materials are loaded onto the bogie using an EOT crane or mechanical devices, and the loaded bogie is moved into the furnace via an electro-mechanical rack-and-pinion or rope-and-drum bogie drive mechanism, ensuring smooth and efficient operation.
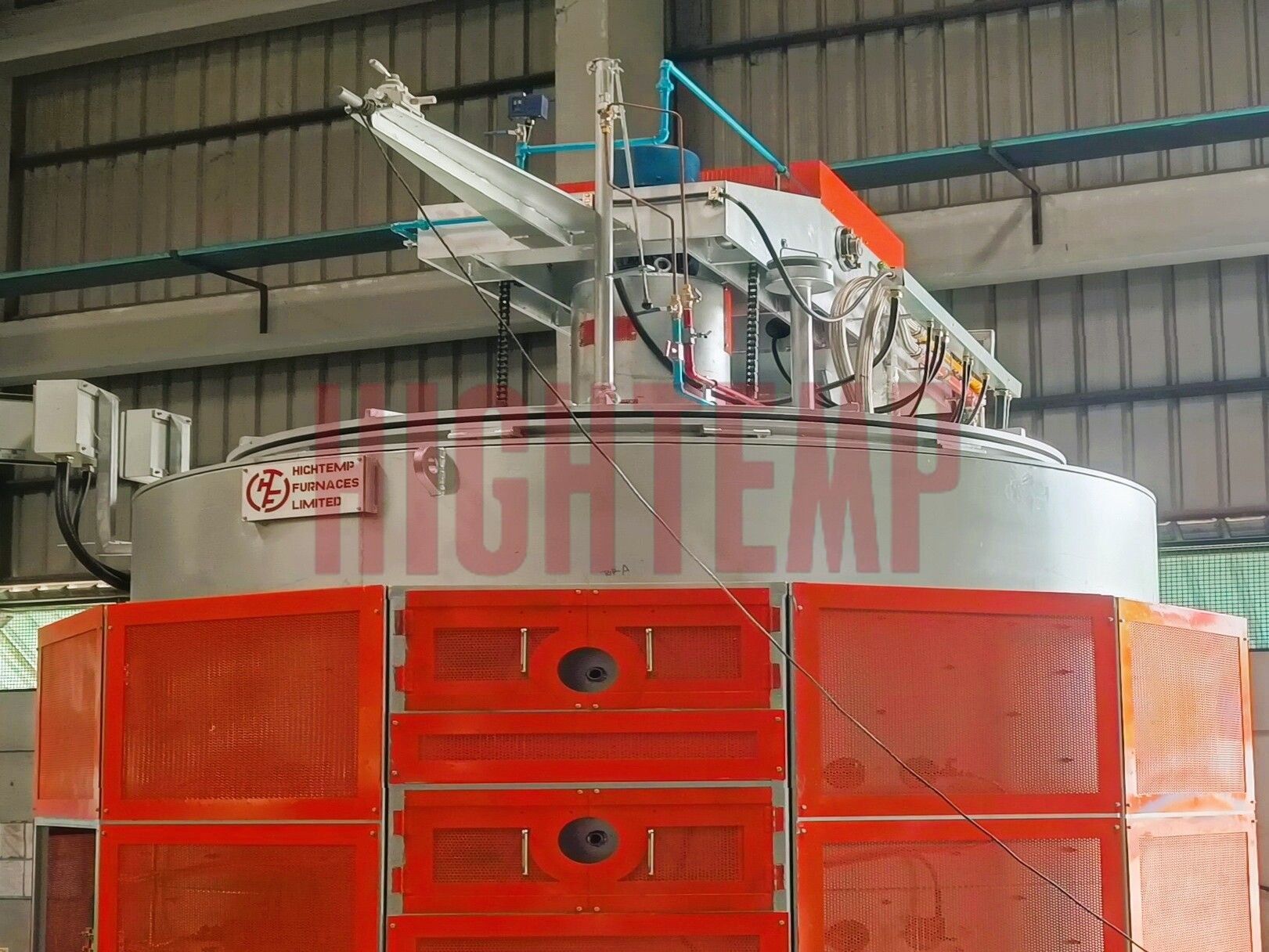
Pit Type Annealing Furnace
HIGHTEMP's Pit Type Annealing Furnace is a specialized heat treatment solution designed for the annealing process, which softens metal components, improves ductility, and relieves internal stresses through controlled heating and cooling. Operating at temperatures typically ranging from 600°C to 900°C, this furnace ensures uniform heat distribution and precise temperature control, critical for achieving an optimal microstructure during the annealing process. The vertical, pit-type design is ideal for treating long, cylindrical, or large components such as shafts, spindles, and forged parts, making it widely used in industries like automotive, aerospace, and heavy engineering. HIGHTEMP’s Pit Type Annealing Furnace combines energy efficiency, reliability, and consistent results, meeting the stringent demands of modern manufacturing processes.