- Delivers deep cleaning, even in components with complex geometries and fine tolerances.
- Aligns with furnace production rates, handling up to 600 kg in continuous operations.
- Suitable for automotive, aerospace, and industrial components like gears, bearings, and shafts.
- Low operational costs and reduced cleaning agent consumption for maximum efficiency.
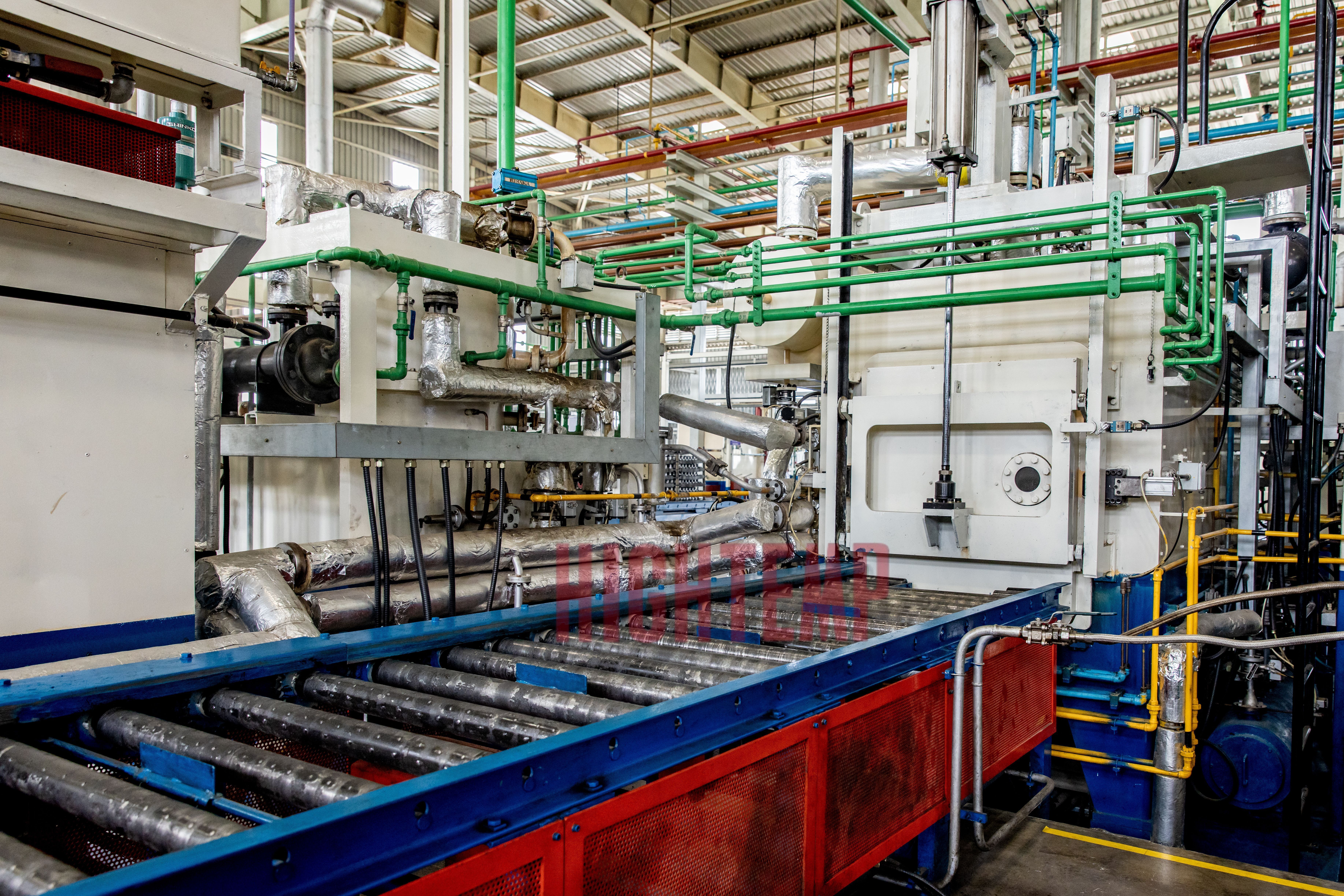

HIGHTEMP's Vacuum Washing Machine 720 is a cutting-edge cleaning system designed to support carburising and quenching processes, ensuring clean and residue-free components for superior heat treatment results. In carburising, where carbon is diffused into the surface of steel, and in quenching, where components are rapidly cooled to enhance hardness, cleanliness plays a vital role in achieving uniform surface properties and avoiding defects. The Vacuum Washing Machine 720 utilizes advanced vacuum-assisted technology to remove oils, grease, and contaminants from components, including gears, shafts, and automotive parts. This ensures that the parts are optimally prepared for carburising and quenching, reducing the risk of scaling, oxidation, or uneven treatment. With a robust design, the Vacuum Washing Machine 720 is engineered for high-capacity operations. It seamlessly integrates into batch and continuous furnace systems, handling gross loads up to 720 kg per batch. This high throughput capability makes it ideal for demanding industrial environments requiring consistent cleaning and reliable performance.
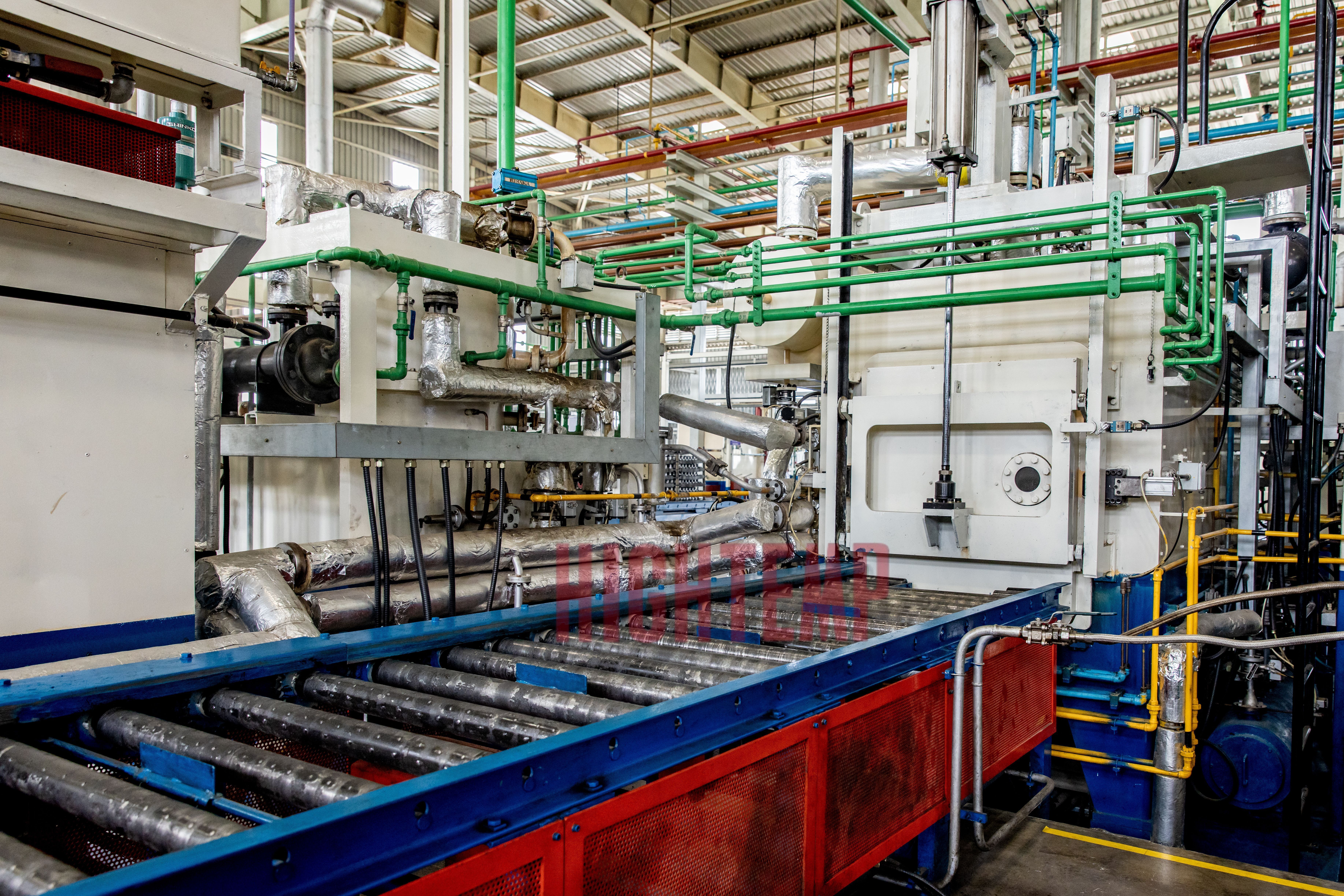

HIGHTEMP's Vacuum Washing Machine 1000 is an advanced cleaning solution tailored for components undergoing carbonitriding and quenching processes. Carbonitriding involves enriching the surface of steel with carbon and nitrogen to enhance hardness, wear resistance, and fatigue strength, while quenching ensures the material achieves the desired hardness by rapid cooling. The efficiency and effectiveness of these processes rely significantly on the cleanliness of the components. The Vacuum Washing Machine 1000 uses state-of-the-art vacuum-assisted cleaning technology to remove oil, grease, and surface contaminants, ensuring parts are thoroughly prepared for carbonitriding and quenching. Its high cleaning performance supports the treatment of critical components such as gears, fasteners, and shafts, resulting in uniform surface properties and minimal defects.
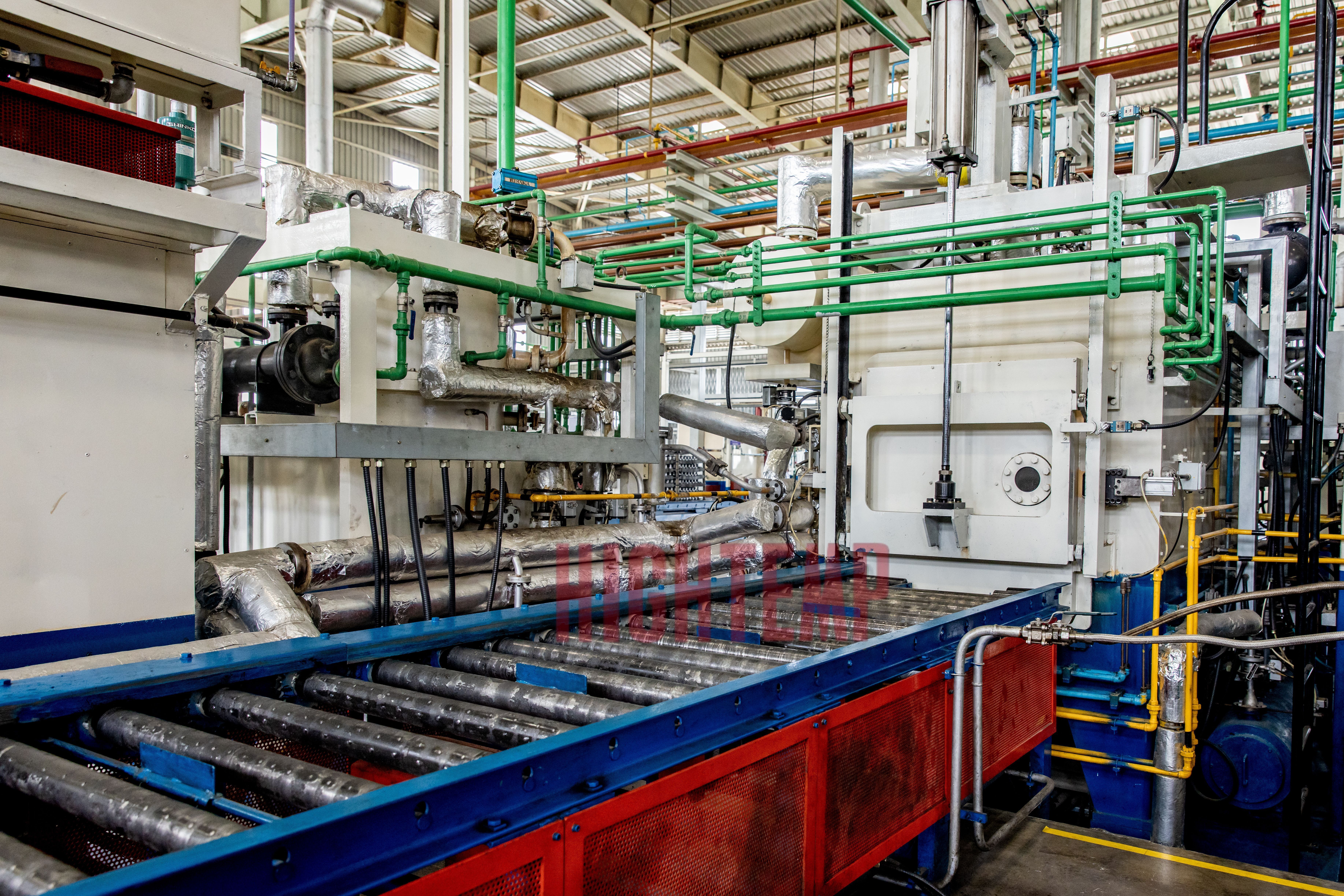

HIGHTEMP's Vacuum Washing Machine 1200 is a high-performance cleaning system designed to meet the rigorous demands of components undergoing austempering and quenching processes. Austempering is a heat treatment process that transforms steel or iron into a bainitic structure, enhancing toughness, strength, and wear resistance. Quenching ensures rapid cooling of the components to achieve the desired microstructure. To ensure precise results, component cleanliness is critical before heat treatment. The Vacuum Washing Machine 1200 employs advanced vacuum-assisted cleaning technology to thoroughly remove oils, grease, and contaminants from components such as springs, gears, and other automotive or industrial parts. Its robust cleaning capabilities prepare components for uniform austempering and quenching, minimizing the risk of defects like scaling or inconsistent microstructure.