- Optimized for facilities with limited floor space, ideal for long or cylindrical components.
- Ensures consistent thermal exposure, enhancing material properties and dimensional accuracy.
- Built with high-quality materials to withstand long operating cycles and harsh environments.
- Tailored to specific industrial needs, including size, capacity, and automation.
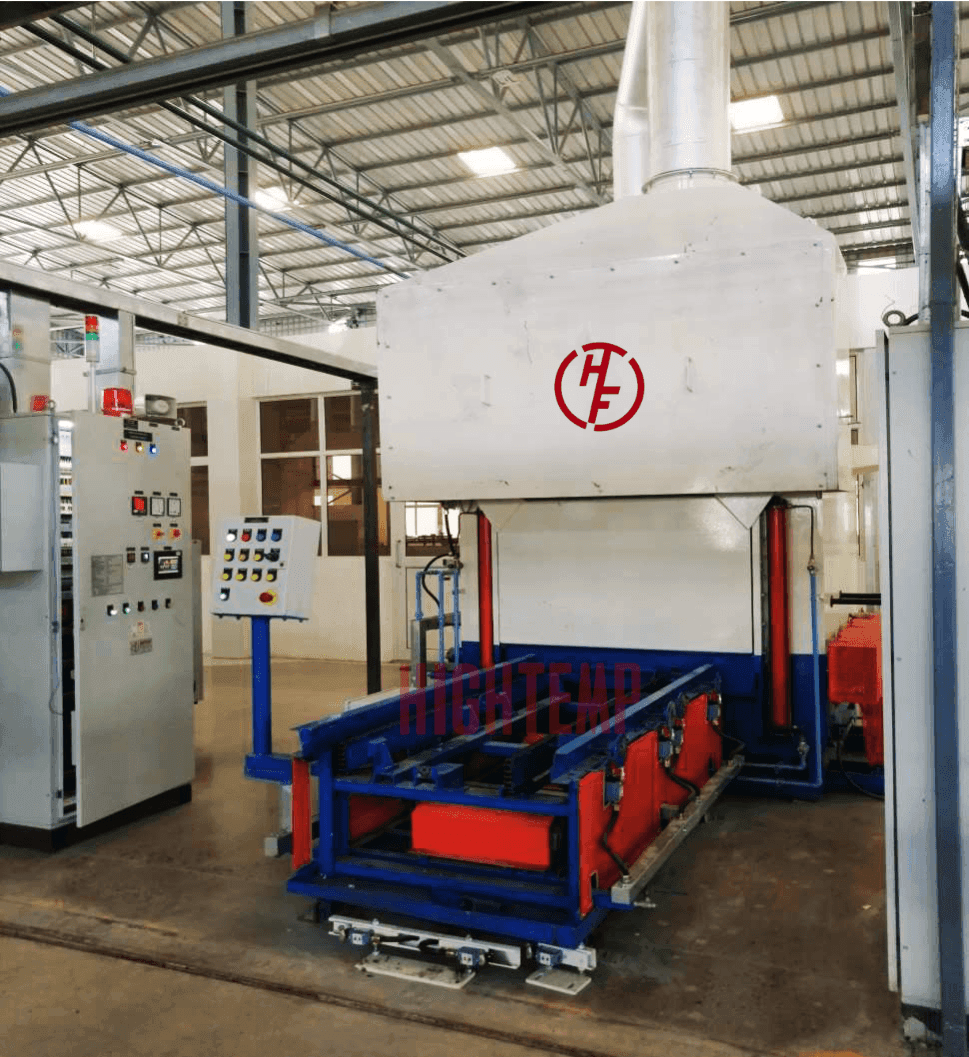

HIGHTEMPs Tempering Furnaces is a Chamber Furnace designed for operating at temperatures ranging from 100°C to 650°C to achieve desired mechanical properties. It also features production capacities ranging from 200 kg to 2500 kg gross per batch. The heating and circulation system ensures uniform heat distribution, for every steel parts in industries such as automotive, aerospace, and manufacturing, ensuring precise temperature control, energy efficiency, and reliable performance.
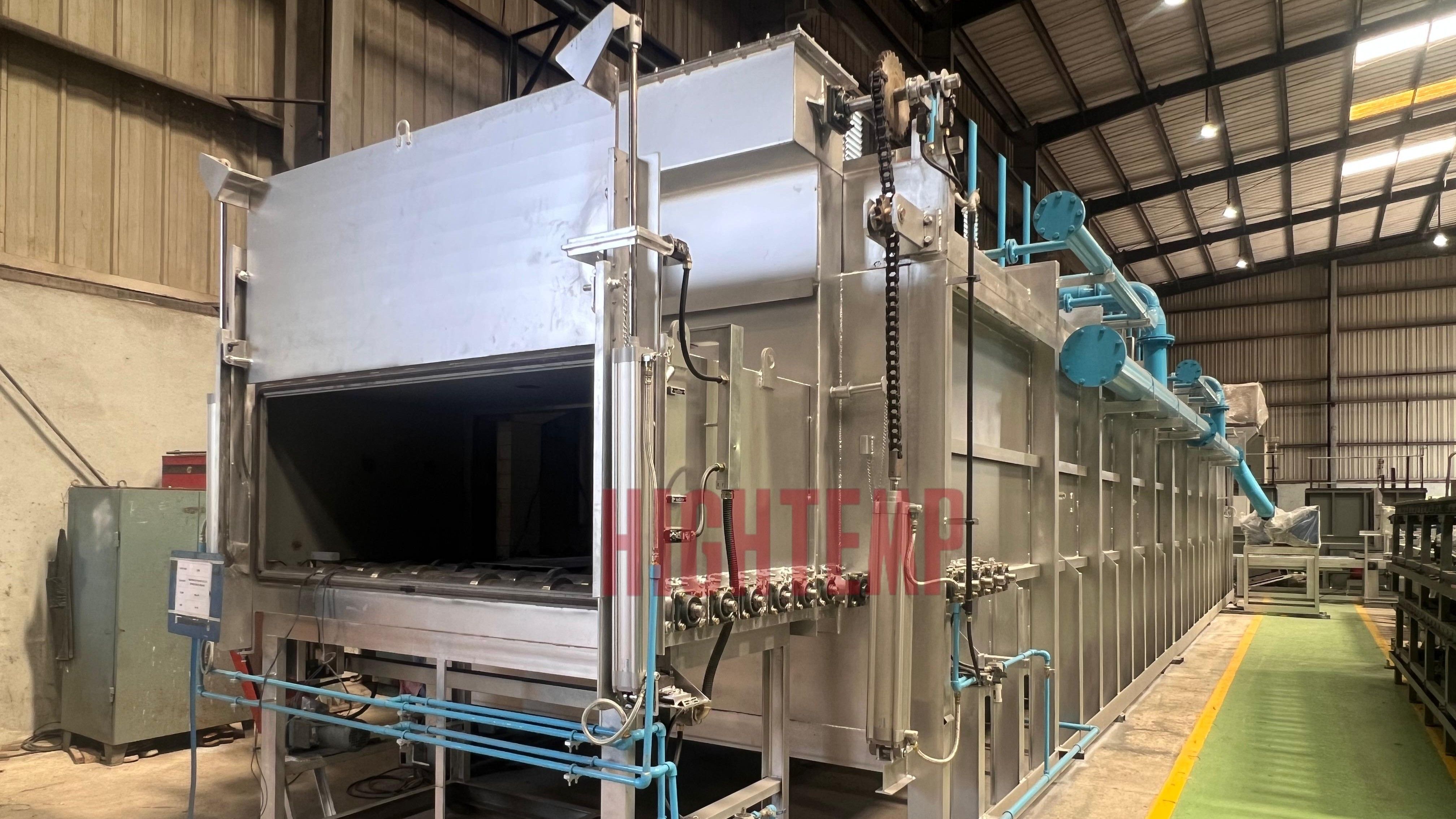

HIGHTEMP’s Annealing Furnaces offer precise control over time and temperature, enhancing properties like machinability, dimensional stability, and electrical and mechanical characteristics in both ferrous and non-ferrous alloys. Primarily used for steel, 40 to 50 seconds, with a 1.5-hour heating and 1-hour soaking the process relieves internal stresses and creates a more uniform structure, also improving workability in metals, glass, and other materials. The furnace features a dedicated charging machine that uses an EOT crane to load S.S. coils onto the hearth, and after the heating cycle, the machine places them in the quench tank. The quenching is completed within cycle time for optimal results.
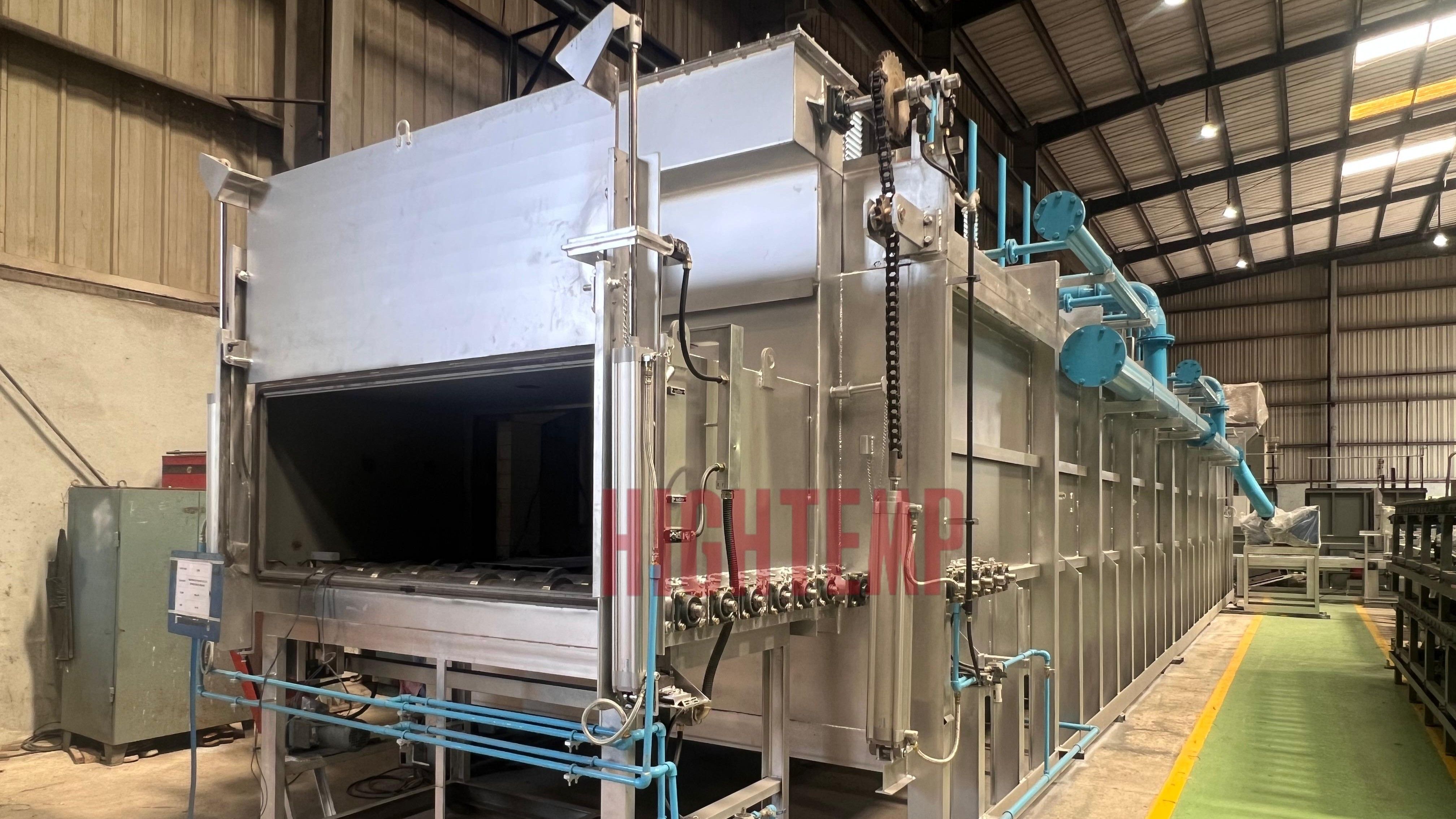

At HIGHTEMP, our Isothermal Annealing Furnaces are engineered to process materials such as carbon steels (e.g., AISI 1040, 1050), alloy steels (e.g., 4140, 4340), cast iron (e.g., grey and ductile iron), and stainless steels (e.g., 304, 316) by heating them to temperatures between 700°C and 900°C, holding them at an isothermal phase to achieve uniform microstructures, and cooling them in a controlled manner. This process reduces hardness, enhances machinability, and improves mechanical properties for components such as gears, shafts, bearings, and engine blocks, meeting the high standards of the automotive, aerospace, and manufacturing industries.