
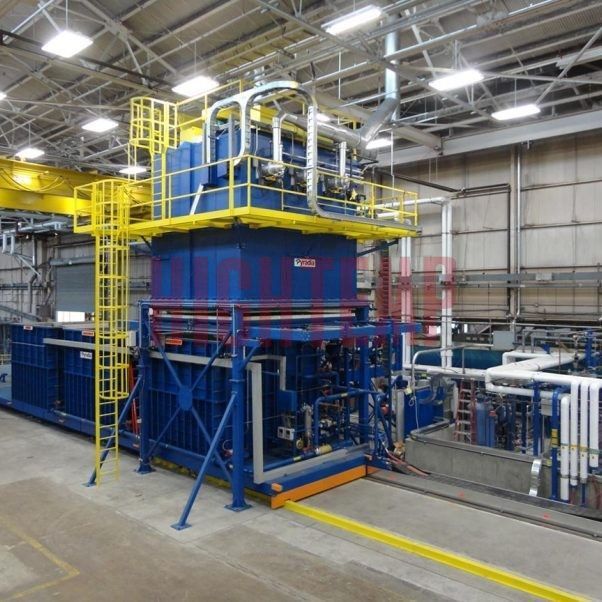
A Drop Bottom Furnace (DBF) is an industrial furnace used for various heat treatment processes. HIGHTEMP’s DBF consists of the furnace chamber, drop bottom and a quenching tank. The key feature is that the furnace is placed above so that the quenching tank can be positioned directly below the furnace.
Safety
Quality Tested
Automation
Models Available
Specifications
Machinery frames are weldments of thick wall tubular steel and prime quality MS plates and structural members.
HIGHTEMP offers an empty furnace and charges soaking options to be selected by the customer. Additionally, PLC and SCADA systems can be modified as per customer requirements.
Furnace heating power is 600kW.
The main quench tank outlet connecting to the chiller is provided with fully stainless steel. The quench tank temperature can be set between 18ºC to 36ºC.
Operating Oven temperature ranges between 35ºC to 600ºC.
Empty furnaces can heat up to 600ºC in 120 minutes. A stabilisation time of 20 to 30 minutes is required to be allotted.
Load basket framework is as per Pyradia design, and a gate for entering into the basket and partition slots for easy loading is provided
Types
Electrically Heated
The Electric option for the DBF uses electrically heated elements to generate heat within the chamber. This offers precise temperature control for consistent heating and cleaner operation. This is often used in operations where electrical power is more practical than gas.
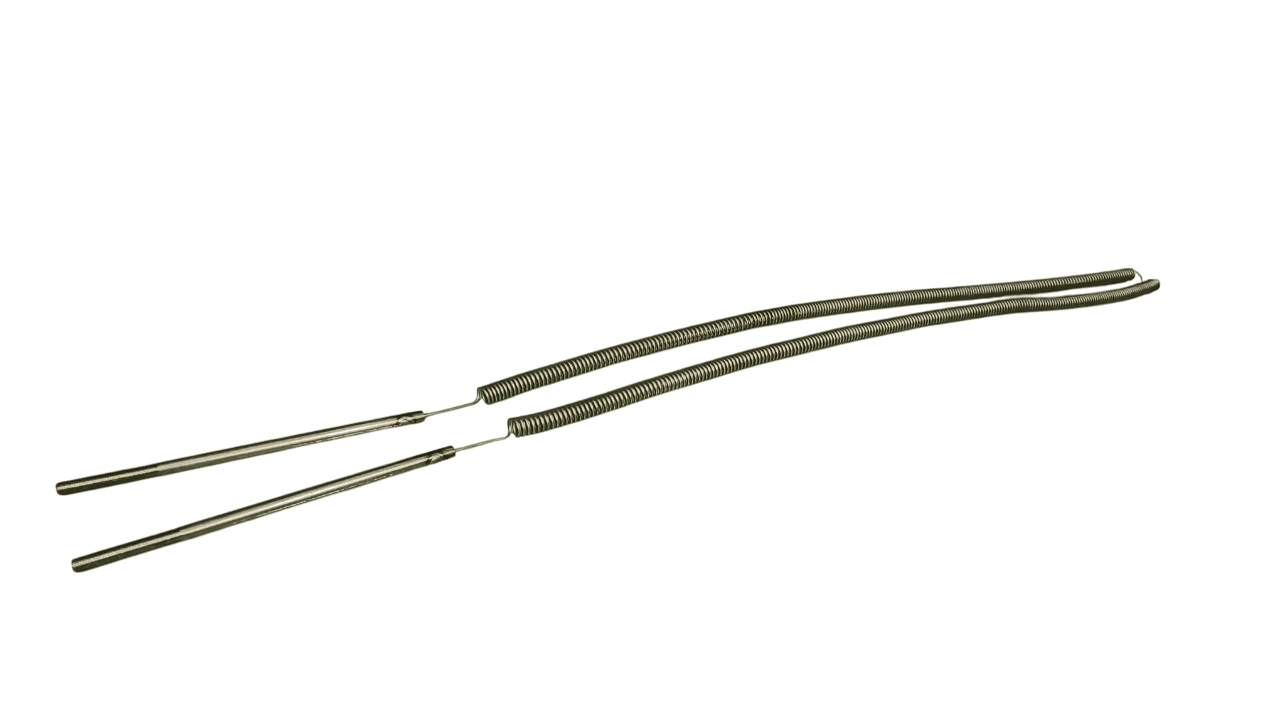
Advantages

Easy Loading and Unloading
The drop-bottom design allows for easy loading and unloading of materials. This is especially beneficial for large or heavy components and to improve operational efficiency.

Drop Quenching Process
HIGHTEMP’s design of the DBF allows for the basket with the components to be lowered into the quenching tank directly. This ensures versatility for handling various component sizes.

Minimized downtime between cycles
HIGHTEMP’s design allows for the efficient transfer of material in and out of the furnace. This minimizes the downtime between processing cycles and can improve the overall productivity.

Large Volume Processing
The efficient loading and unloading process in the DBF supports continuous processing, making it suitable for large-scale industrial operations.

Custom options for the furnace
HIGHTEMP offers customizable options for soaking time and SCADA System, which is tailored to the customer’s requirements.
Industries Served
Aerospace Industry
The Aerospace Industry benefits from HIGHTEMP’s Drop Bottom Furnace as it helps enhance the properties of critical components. It can help enhance the performance, durability, and quality of a wide range of components.
Material Grades Available
- Titanium Alloys - Ti-6Al-4V, Ti-6Al-4V ELI, Ti-5Al-2.5Sn
- Aluminium Alloys - 7075, 6061, 2024
- Stainless Steel - AISI 304, AISI 316, 17-4PH
Parts
Wing Spars, Fuselage Frames, Turbine Blades, Nozzle Guide Vanes, Struts, Pistons, Fasteners, Actuators
Applications
Why Choose Hightemp

HIGHTEMP is India’s No 1 manufacturer of Heat Treatment Furnaces and Commercial Heat Treatment.

HIGHTEMP equips the furnaces with technologies such as SCADA, FURNACE 4.0 (IoT-enabled Furnaces), and Allen Bradley PLC System.

Safety features of the Drop Bottom Furnace include thermocouple, pressure switch, safety guarding, alarms, and other safety devices. The safety equipment is as per International standards and Factories Act of India.
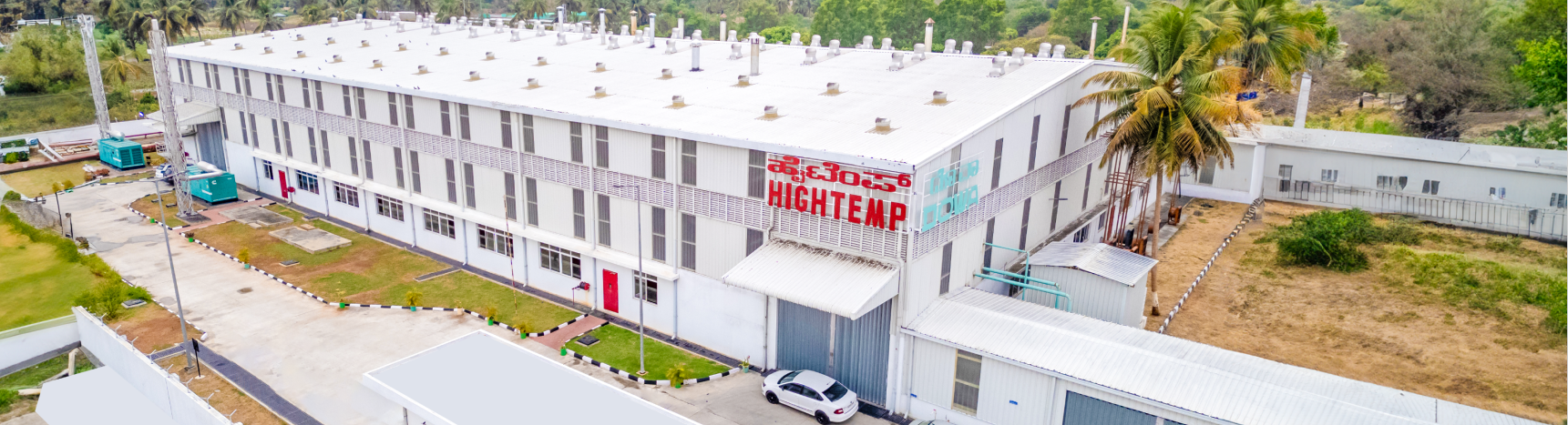
Our Clients
Are you interested in our
Drop Bottom Furnace ?
Please, read the answers to frequently asked questions about our products.
A drop bottom furnace operated by allowing the furnace floor to be removed, providing easy access to the chamber for loading and unloading materials. The furnace heats the materials using burners/electrically heated parts to achieve the desired temperature. Once the heat treatment process is complete, the quenching tank aligns itself below the furnace chamber, and the components are dropped into the tank.
The main advantage of the Drop Bottom Furnace includes easy loading and unloading of heavy components.
HIGHTEMP’s Drop Bottom Furnace can perform Annealing, Normalizing, Tempering, Hardening, Ageing, and Stress Relieving.
Compared to other furnaces, the Drop Bottom Furnace offers easy handling of materials, especially large components during the loading and unloading process, along with the drop quenching process.