- Consistent Quality: Delivers uniform hardness, toughness, and strength across all components, ensuring reliability and performance.
- High Productivity: Continuous operation enables round-the-clock production, reducing downtime and maximizing throughput.
- Customizable Processes: Tailored settings for temperature, atmosphere, and cycle times make it adaptable to various materials and applications.
- Cost and Energy Savings: Energy-efficient design reduces operational costs while maintaining high performance standards.
- Global Standards Compliance: Adheres to international heat treatment quality standards, ensuring reliability for critical applications.
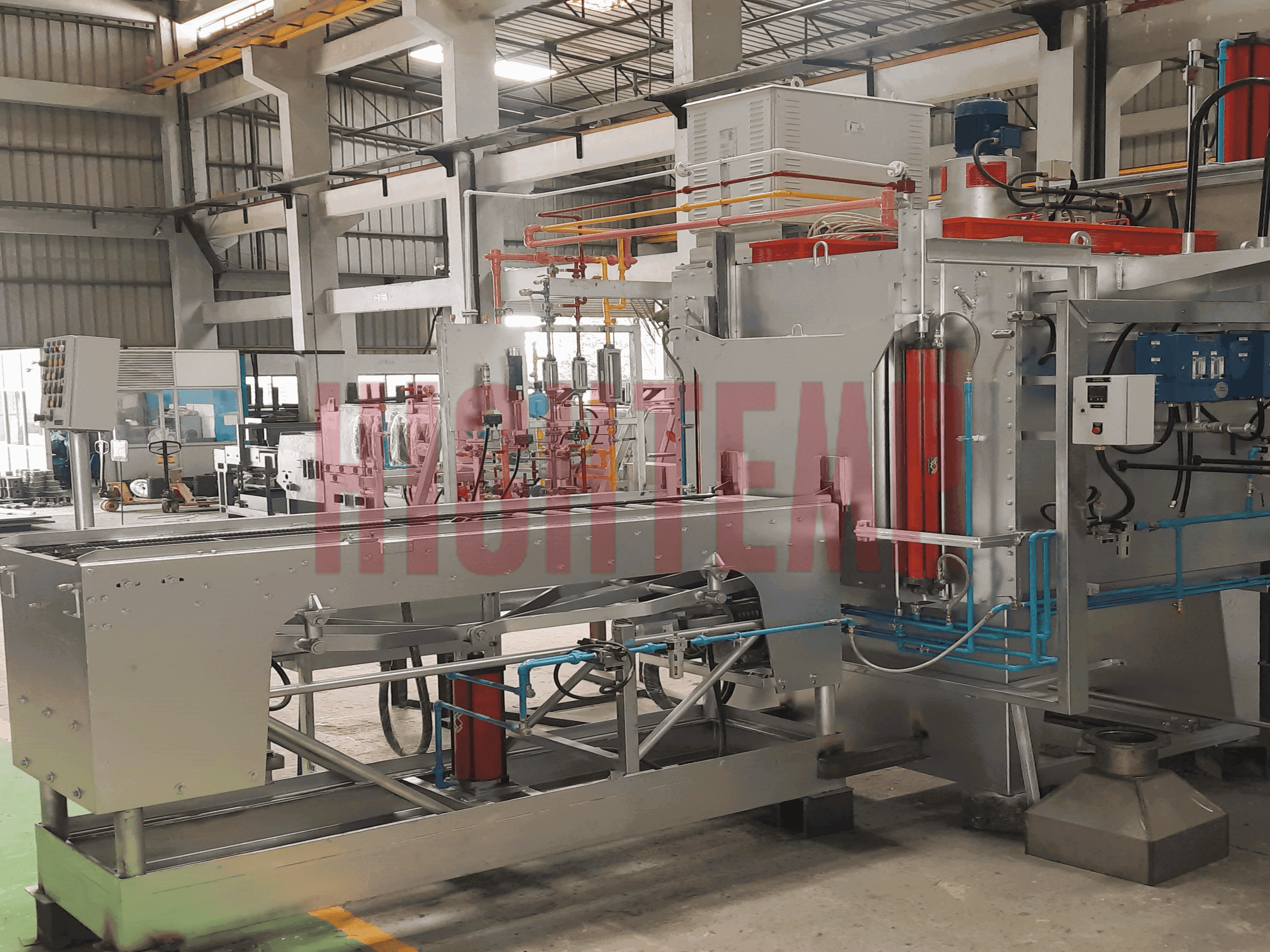

Our Sealed Quench Furnace is ideal for the heat treatment of components like gears, shafts, crankshafts, pins, bolts, fasteners, and tool & die parts. It offers a controlled environment for carburising processes, which are critical for enhancing the mechanical properties of materials such as EN8, EN9, EN19, EN24, 16MnCr5, 20MnCr5, SAE 8620, and EN31. Carburising is used to add carbon to the surface of low-carbon steels to enhance their hardness and wear resistance, while keeping the core material tough and ductile. After carburising, tempering is performed to reduce brittleness and improve the toughness of the hardened surface. It also helps relieve internal stresses that may result from the quenching process. This furnace can perform other heat treatment processes, including hardening, carbonitriding, normalizing, nitrocarburizing, nitriding, austempering, neutral hardening, annealing, and bright hardening.
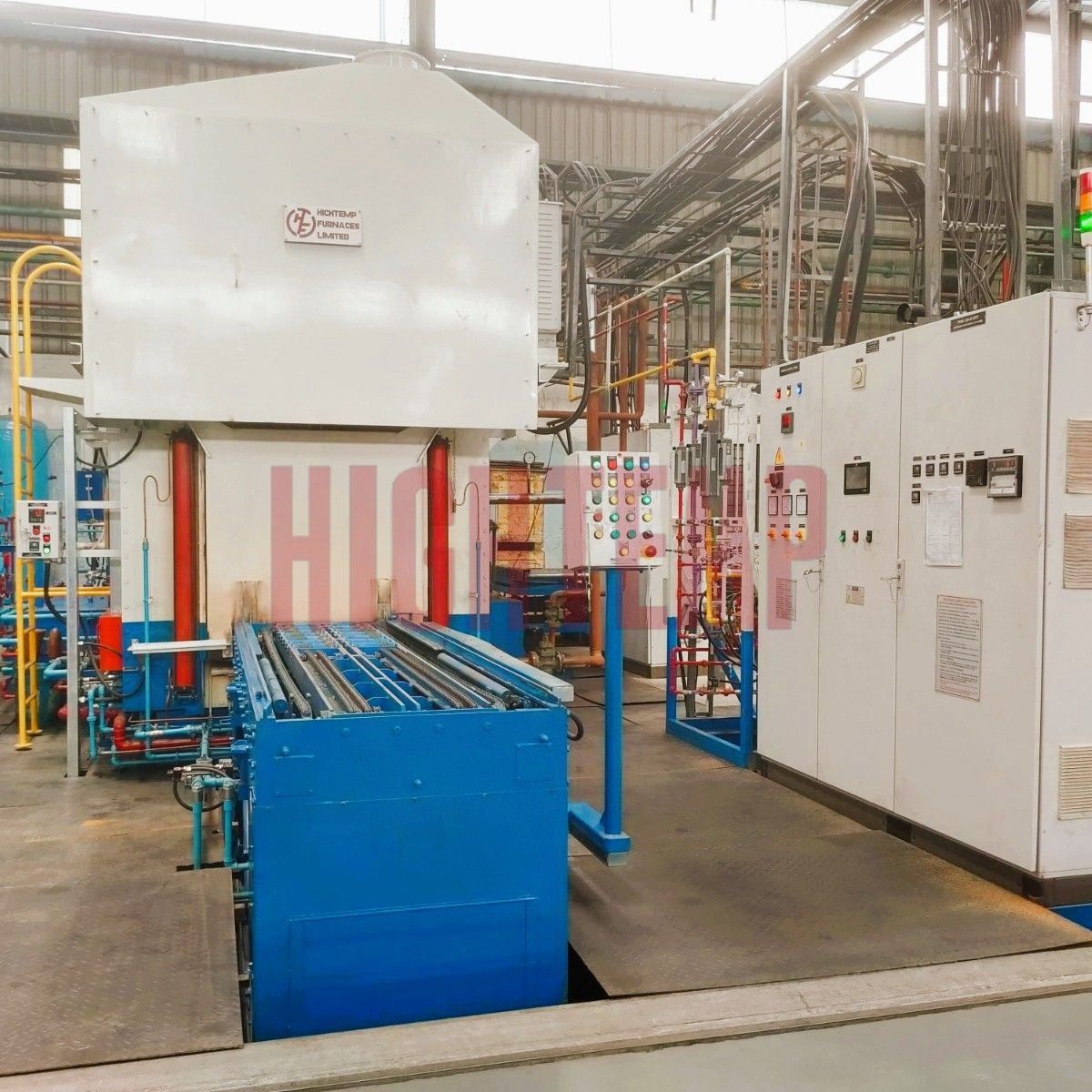

HIGHTEMP Sealed Quench Furnace is the ideal solution for the carbonitriding and tempering of high-performance components, ensuring enhanced surface hardness, wear resistance, and toughness. This furnace is particularly effective for components such as gears, shafts, pins, bolts, fasteners, crankshafts, tool & die parts, and bearings. Using materials like EN8, EN9, EN19, EN24, 16MnCr5, 20MnCr5, SAE 8620, and EN31 (high-carbon steels), it ensures consistent, superior-quality heat treatment. Carbonitriding is a surface hardening process where carbon and nitrogen are diffused into the steel surface, improving its hardness, wear resistance, and fatigue strength. The sealed quench furnace ensures a controlled atmosphere to minimize oxidation and decarburisation. After carbonitriding, tempering is used to relieve internal stresses and reduce brittleness while retaining the hardness of the treated surface. This furnace can perform other heat treatment processes, including carburizing, hardening, normalizing, nitrocarburizing, nitriding, austempering, neutral hardening, annealing, and bright hardening.
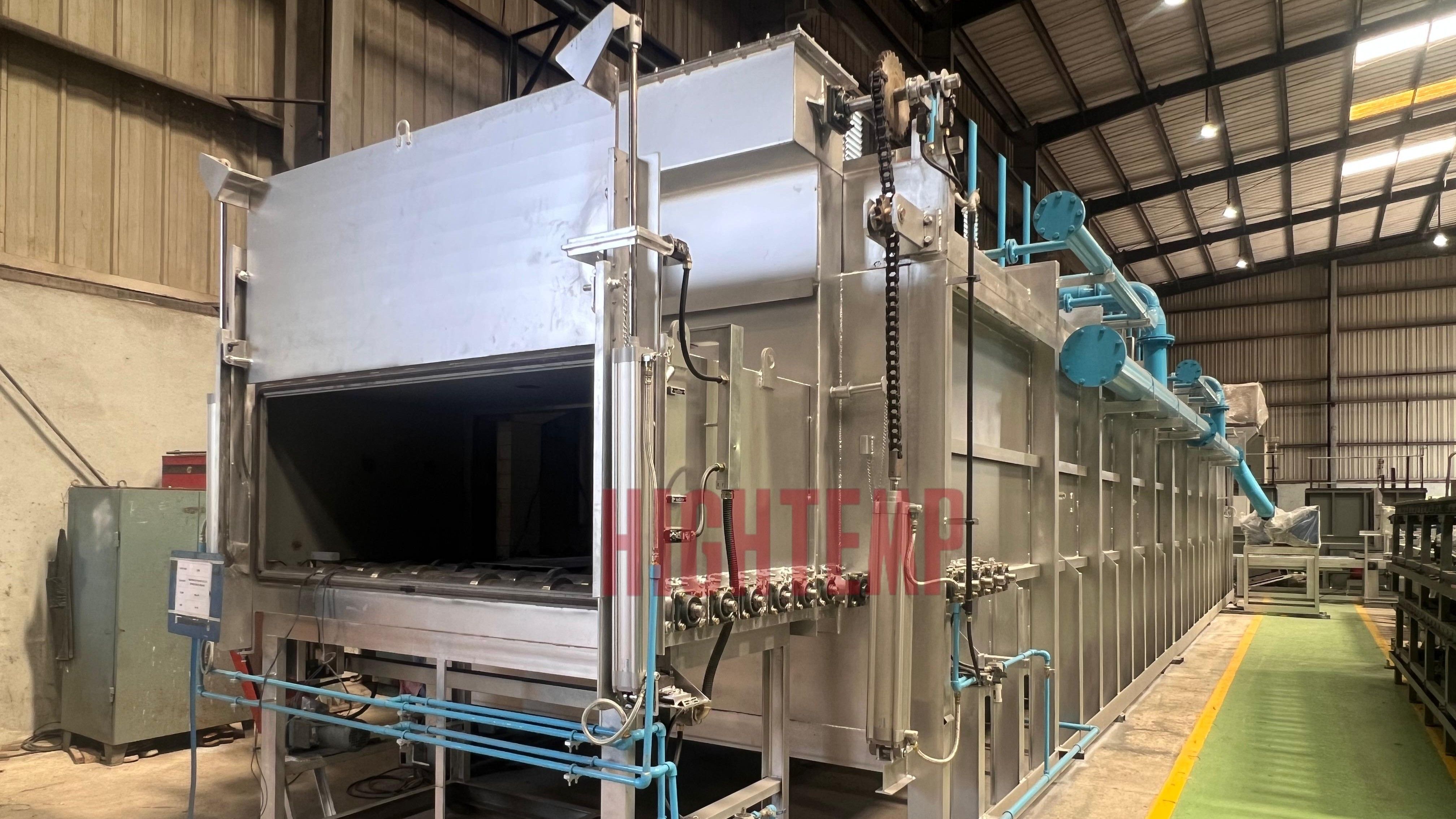

The HIGHTEMP Hardening and Tempering Furnace is an advanced industrial system specifically designed to enhance the mechanical properties of metal components such as gears, shafts, tools, and dies, through a precise process that involves first heating the metals to high temperatures for hardening, followed by a controlled cooling and a subsequent tempering cycle. This dual functionality process significantly increases the hardness and wear resistance of components, while also improving their toughness and fatigue strength. Suitable for a variety of material grades including, but not limited to, 4140 steel, 4340 steel, and AISI D2 tool steel, this furnace is indispensable in industries such as automotive, aerospace, and industrial machinery, where precise and consistent heat treatment is crucial for producing high-performance parts that can withstand extreme conditions and demanding applications. Equipped with advanced control systems for accurate temperature regulation, uniform heating for consistent results, and an energy-efficient design, the HIGHTEMP Hardening and Tempering Furnace optimizes productivity while maintaining stringent quality standards, making it a cost-effective solution for modern manufacturing needs.