- Delivers uniform structural properties across all processed components.
- Improves ease of machining for treated materials, reducing tool wear and improving productivity.
- Protective atmosphere prevents surface degradation and retains material quality.
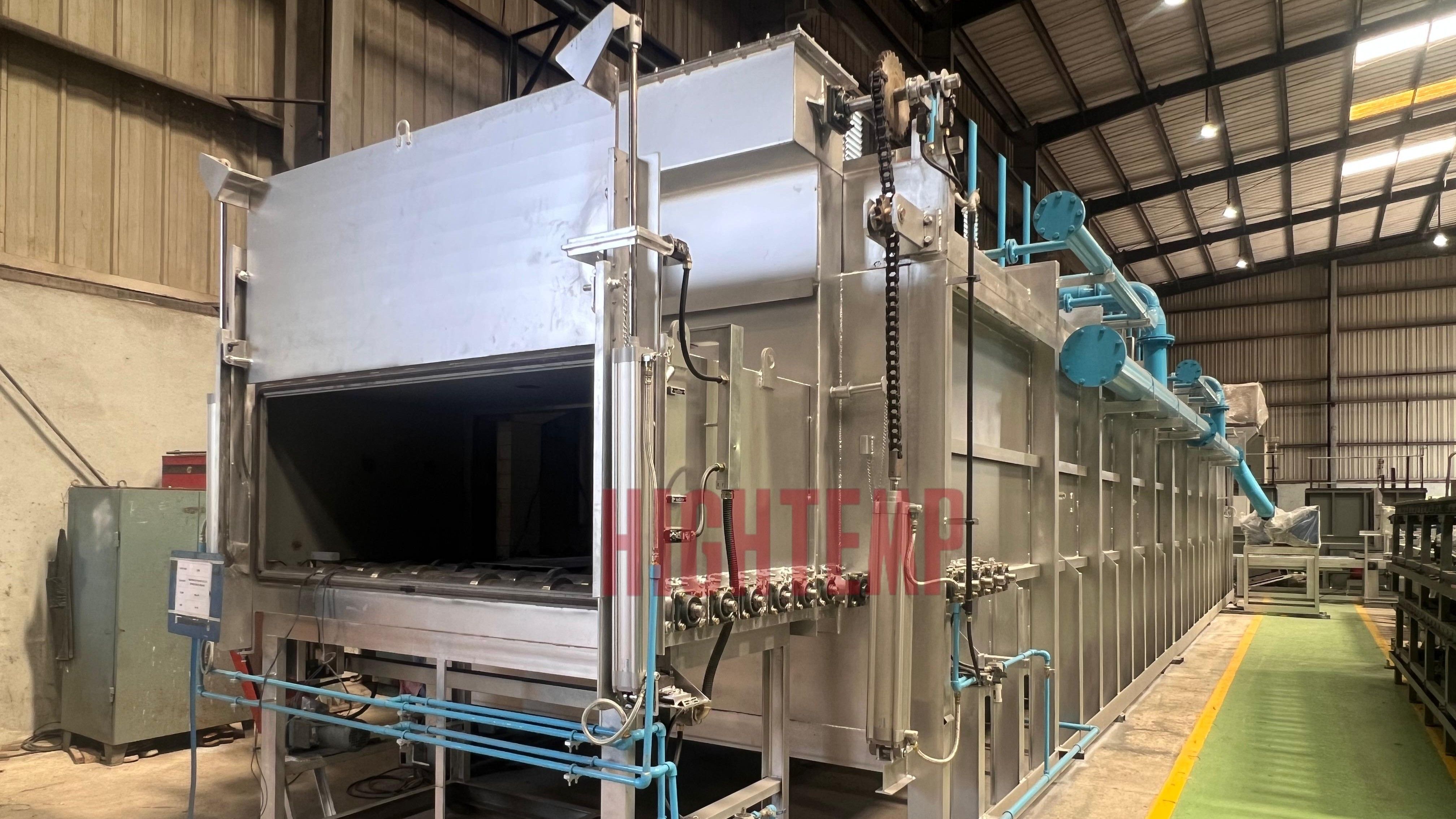

HIGHTEMP’s Annealing Furnaces offer precise control over time and temperature, enhancing properties like machinability, dimensional stability, and electrical and mechanical characteristics in both ferrous and non-ferrous alloys. Primarily used for steel, 40 to 50 seconds, with a 1.5-hour heating and 1-hour soaking the process relieves internal stresses and creates a more uniform structure, also improving workability in metals, glass, and other materials. The furnace features a dedicated charging machine that uses an EOT crane to load S.S. coils onto the hearth, and after the heating cycle, the machine places them in the quench tank. The quenching is completed within cycle time for optimal results.
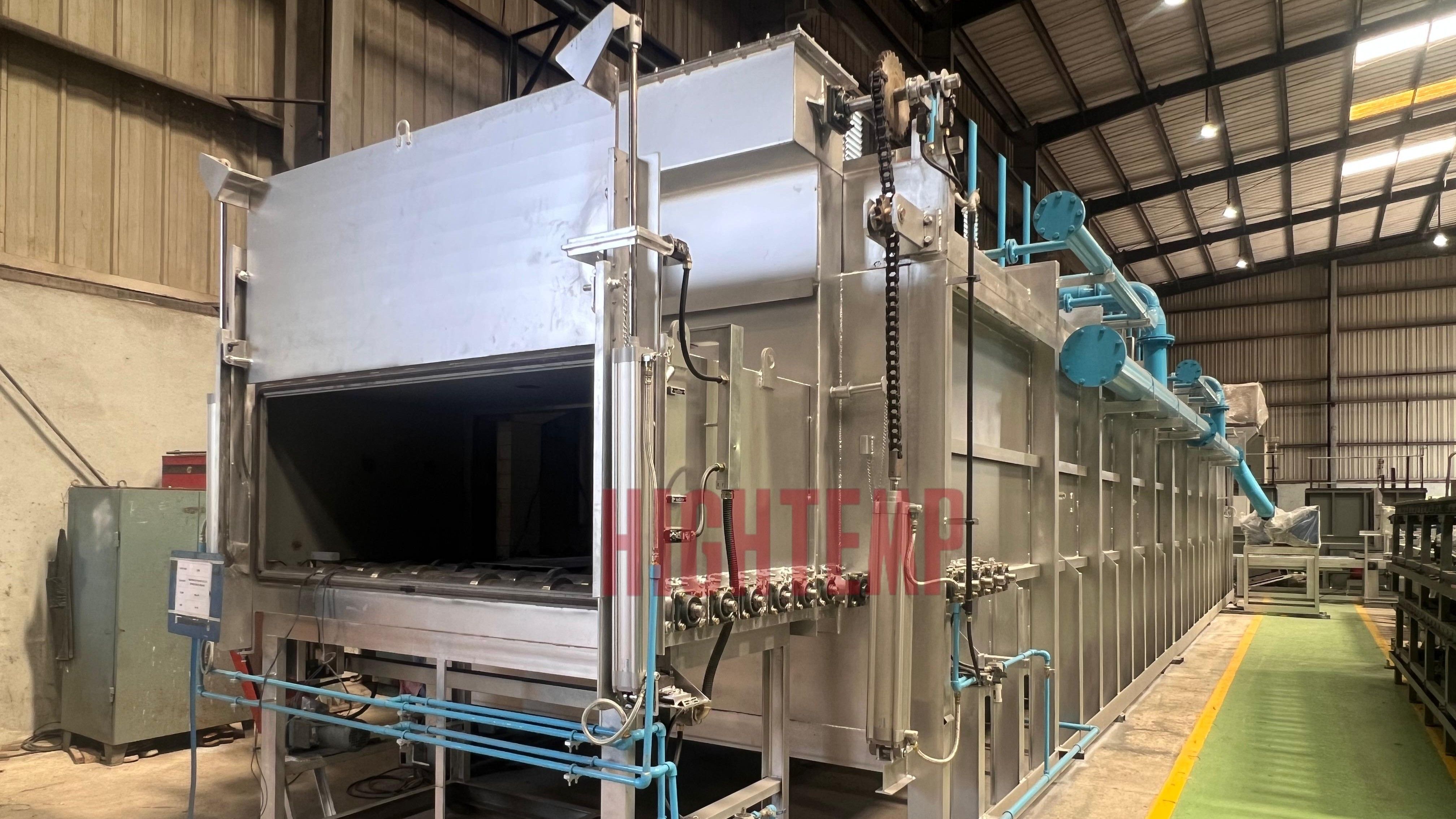

The Spheroidize Annealing Furnace from HIGHTEMP is ideal for treating steels with over 0.8% carbon, operating at 680°C to 750°C to transform cementite into a spheroidal structure within an alpha ferrite matrix. This process restores machinability in work-hardened parts like bearings, fasteners, wire rods, springs, and gears, improving ductility and toughness while reducing hardness and strength. Conducted under a protective endothermic atmosphere to prevent oxidation and decarburization, the furnace supports low, medium, and high-carbon steels (e.g., 1018, 1045, 1080) and alloy steels (e.g., 4140, 4340). With precision temperature control, electric or gas heating, and automated PLC systems, this high-throughput furnace ensures consistent, efficient, and high-quality results for industries like automotive and tool manufacturing.
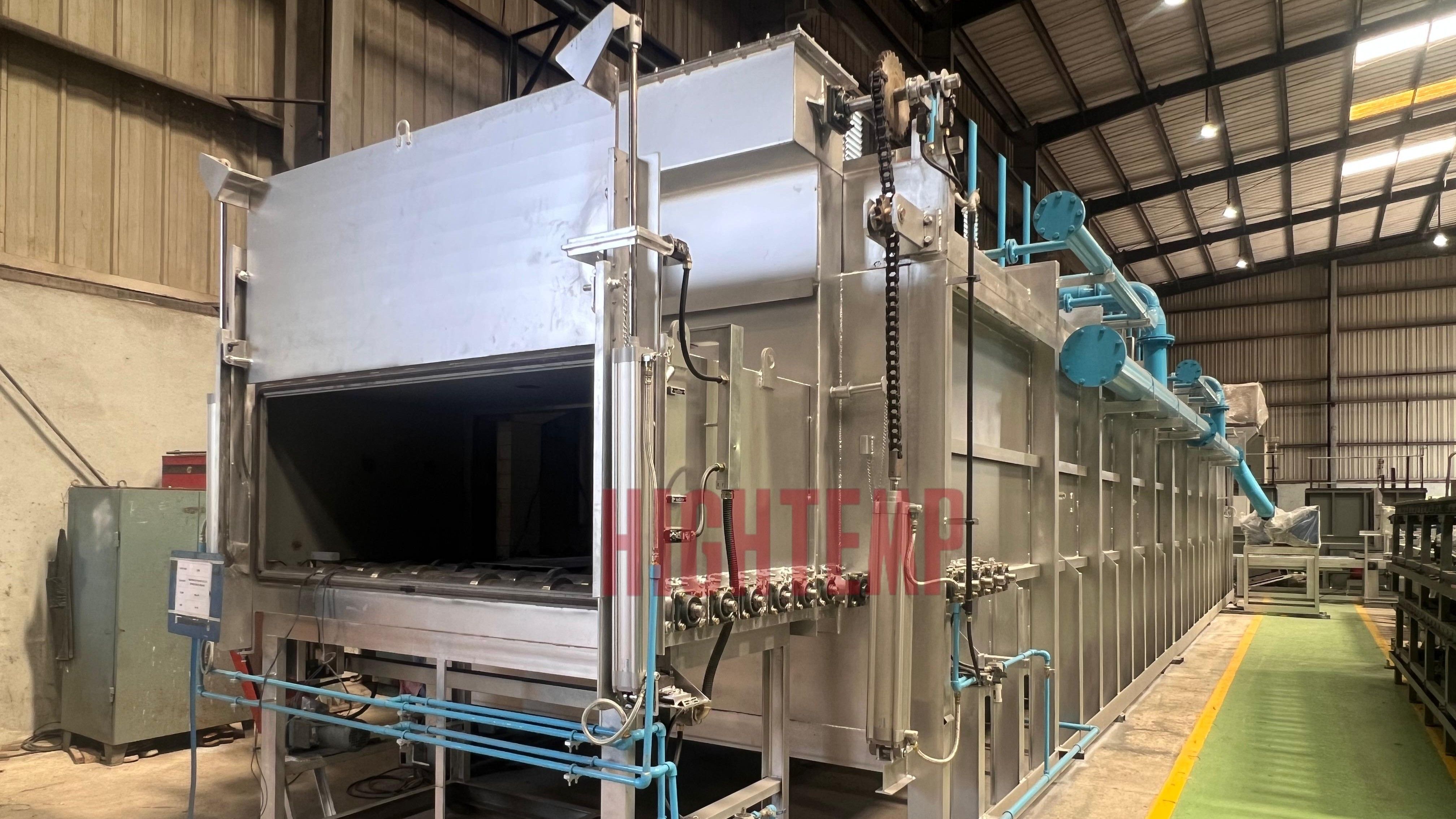

The HIGHTEMP Hardening and Tempering Furnace is an advanced industrial system specifically designed to enhance the mechanical properties of metal components such as gears, shafts, tools, and dies, through a precise process that involves first heating the metals to high temperatures for hardening, followed by a controlled cooling and a subsequent tempering cycle. This dual functionality process significantly increases the hardness and wear resistance of components, while also improving their toughness and fatigue strength. Suitable for a variety of material grades including, but not limited to, 4140 steel, 4340 steel, and AISI D2 tool steel, this furnace is indispensable in industries such as automotive, aerospace, and industrial machinery, where precise and consistent heat treatment is crucial for producing high-performance parts that can withstand extreme conditions and demanding applications. Equipped with advanced control systems for accurate temperature regulation, uniform heating for consistent results, and an energy-efficient design, the HIGHTEMP Hardening and Tempering Furnace optimizes productivity while maintaining stringent quality standards, making it a cost-effective solution for modern manufacturing needs.