- Controlled atmosphere furnaces can reduce emissions and minimize the environmental impact of heat treatment processes.
- The controlled atmosphere helps maintain a clean and pristine surface finish on the treated materials, eliminating the need for additional polishing or finishing steps.
- The ability to precisely control the gas composition and flow rate allows for fine-tuning the heat treatment process, leading to optimal results.
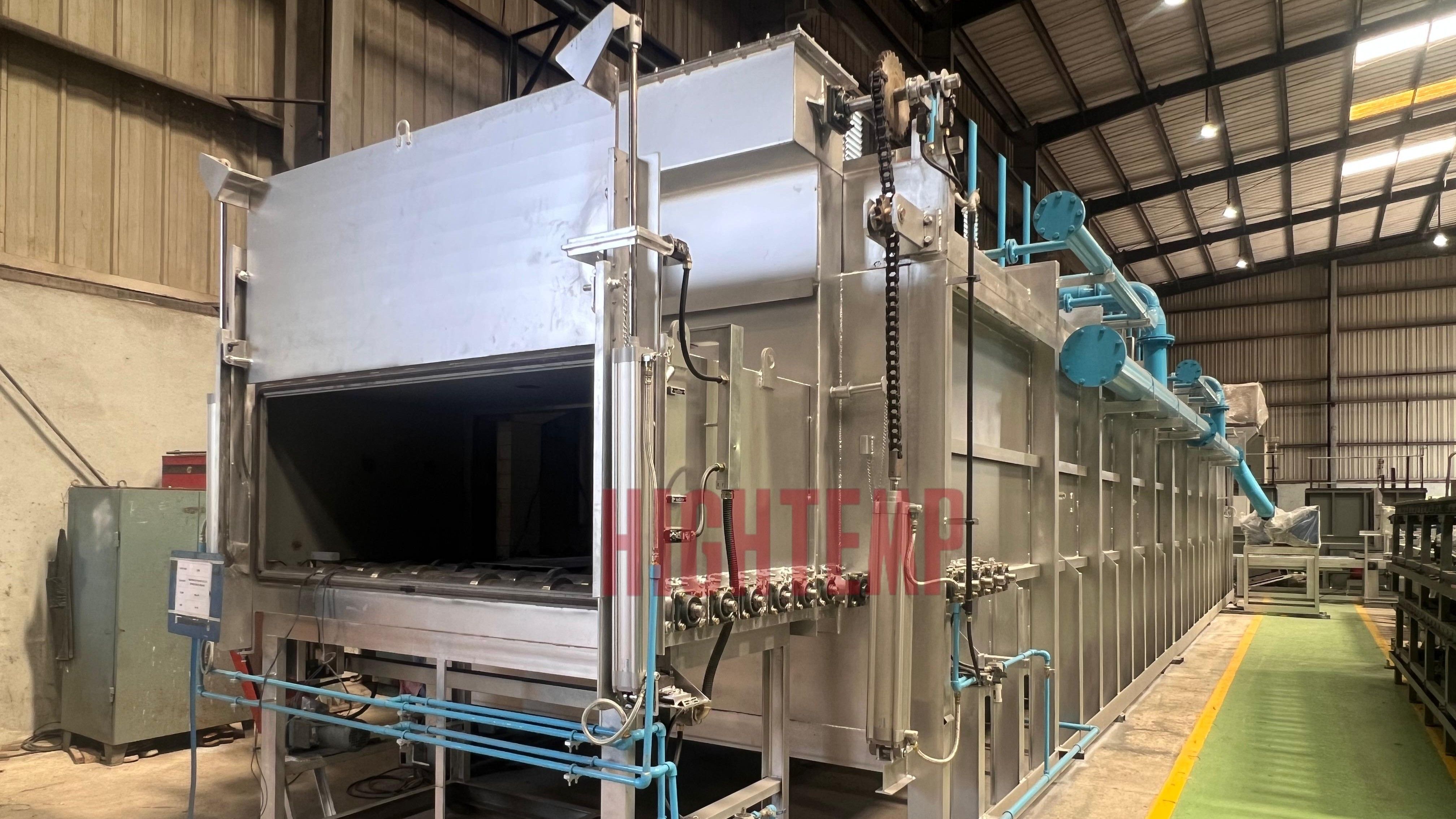

The HIGHTEMP Carburising and Hardening Furnace is an advanced industrial furnace specifically engineered to enhance the surface hardness and wear resistance of metal components. It utilizes a combination of carburising, where carbon is diffused into the surface layer of the metal in a precisely controlled atmosphere to significantly increase its hardness, and hardening, which involves uniform heating to a high temperature followed by rapid quenching. This process locks in the hard surface layer while maintaining a tough and ductile core. It is an indispensable tool for critical applications in various sectors such as automotive, aerospace, and industrial machinery, where components must possess exceptional durability and performance to withstand extreme conditions and high-stress environments.
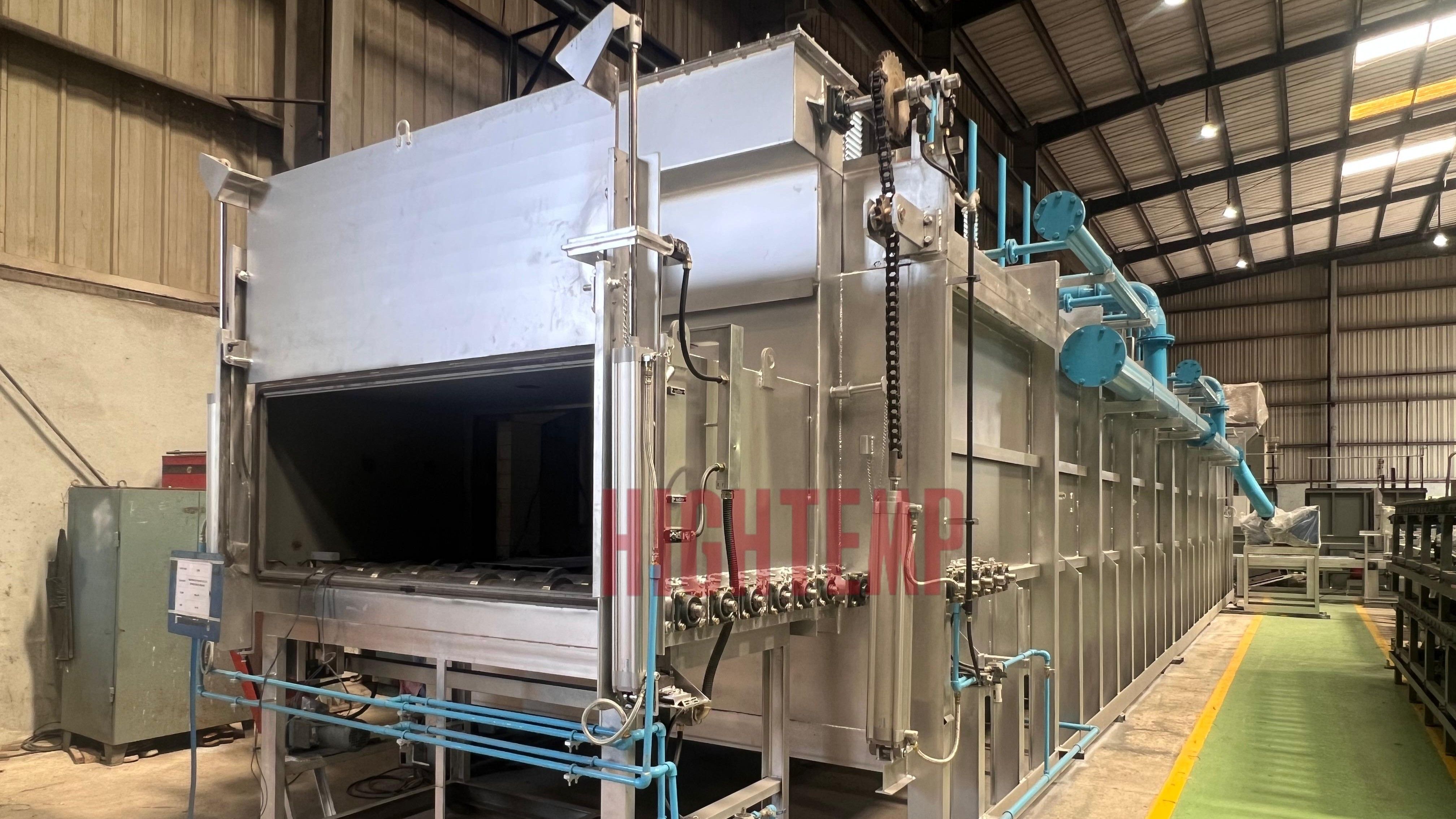

The Spheroidize Annealing Furnace from HIGHTEMP is ideal for treating steels with over 0.8% carbon, operating at 680°C to 750°C to transform cementite into a spheroidal structure within an alpha ferrite matrix. This process restores machinability in work-hardened parts like bearings, fasteners, wire rods, springs, and gears, improving ductility and toughness while reducing hardness and strength. Conducted under a protective endothermic atmosphere to prevent oxidation and decarburization, the furnace supports low, medium, and high-carbon steels (e.g., 1018, 1045, 1080) and alloy steels (e.g., 4140, 4340). With precision temperature control, electric or gas heating, and automated PLC systems, this high-throughput furnace ensures consistent, efficient, and high-quality results for industries like automotive and tool manufacturing.
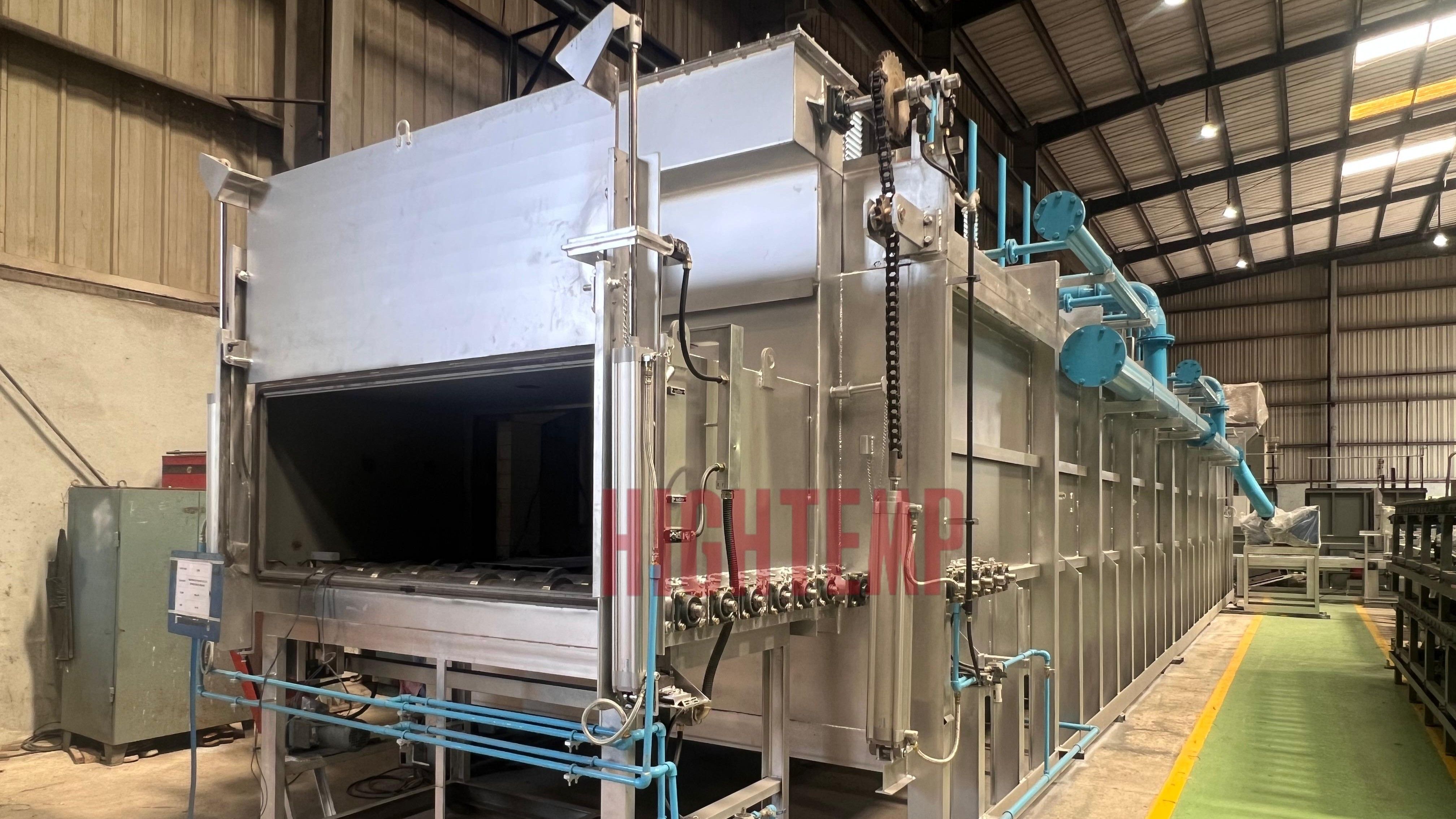

At HIGHTEMP, our Isothermal Annealing Furnaces are engineered to process materials such as carbon steels (e.g., AISI 1040, 1050), alloy steels (e.g., 4140, 4340), cast iron (e.g., grey and ductile iron), and stainless steels (e.g., 304, 316) by heating them to temperatures between 700°C and 900°C, holding them at an isothermal phase to achieve uniform microstructures, and cooling them in a controlled manner. This process reduces hardness, enhances machinability, and improves mechanical properties for components such as gears, shafts, bearings, and engine blocks, meeting the high standards of the automotive, aerospace, and manufacturing industries.