- The furnace is equipped with a sturdy and proven refractory lining pattern, providing enhanced heat retention and long service life.
- Capacity range of 1 ton to 4 tons per batch, making it suitable for both small-scale and large-scale production.
- Sturdy, energy-efficient construction ensures optimal fuel consumption, reducing operational costs.
- Includes a fully equipped system with charging machine, quenching mechanism, and chimney, offering a comprehensive solution.
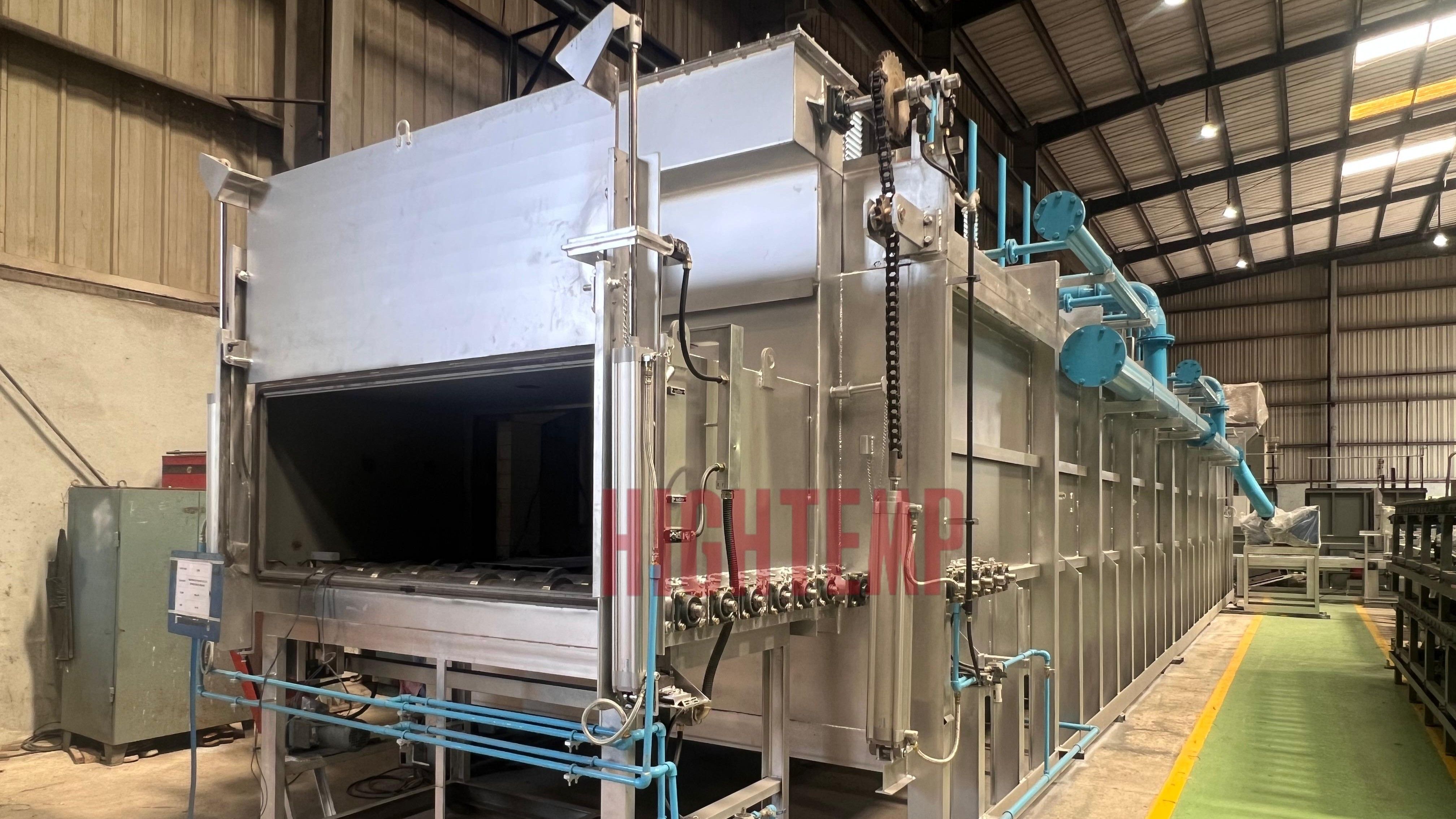

The HIGHTEMP Hardening and Tempering Furnace is an advanced industrial system specifically designed to enhance the mechanical properties of metal components such as gears, shafts, tools, and dies, through a precise process that involves first heating the metals to high temperatures for hardening, followed by a controlled cooling and a subsequent tempering cycle. This dual functionality process significantly increases the hardness and wear resistance of components, while also improving their toughness and fatigue strength. Suitable for a variety of material grades including, but not limited to, 4140 steel, 4340 steel, and AISI D2 tool steel, this furnace is indispensable in industries such as automotive, aerospace, and industrial machinery, where precise and consistent heat treatment is crucial for producing high-performance parts that can withstand extreme conditions and demanding applications. Equipped with advanced control systems for accurate temperature regulation, uniform heating for consistent results, and an energy-efficient design, the HIGHTEMP Hardening and Tempering Furnace optimizes productivity while maintaining stringent quality standards, making it a cost-effective solution for modern manufacturing needs.
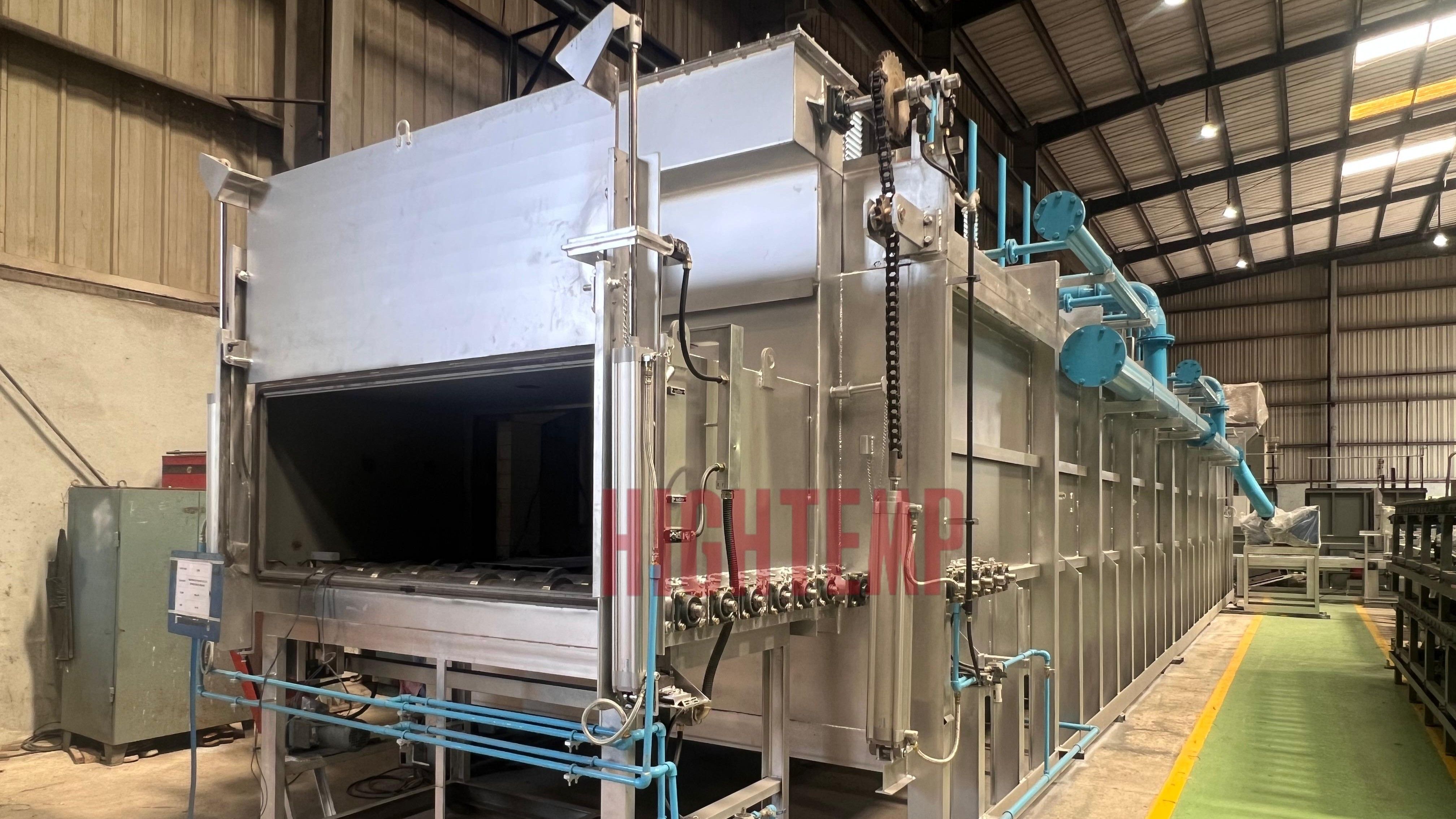

The Spheroidize Annealing Furnace from HIGHTEMP is ideal for treating steels with over 0.8% carbon, operating at 680°C to 750°C to transform cementite into a spheroidal structure within an alpha ferrite matrix. This process restores machinability in work-hardened parts like bearings, fasteners, wire rods, springs, and gears, improving ductility and toughness while reducing hardness and strength. Conducted under a protective endothermic atmosphere to prevent oxidation and decarburization, the furnace supports low, medium, and high-carbon steels (e.g., 1018, 1045, 1080) and alloy steels (e.g., 4140, 4340). With precision temperature control, electric or gas heating, and automated PLC systems, this high-throughput furnace ensures consistent, efficient, and high-quality results for industries like automotive and tool manufacturing.
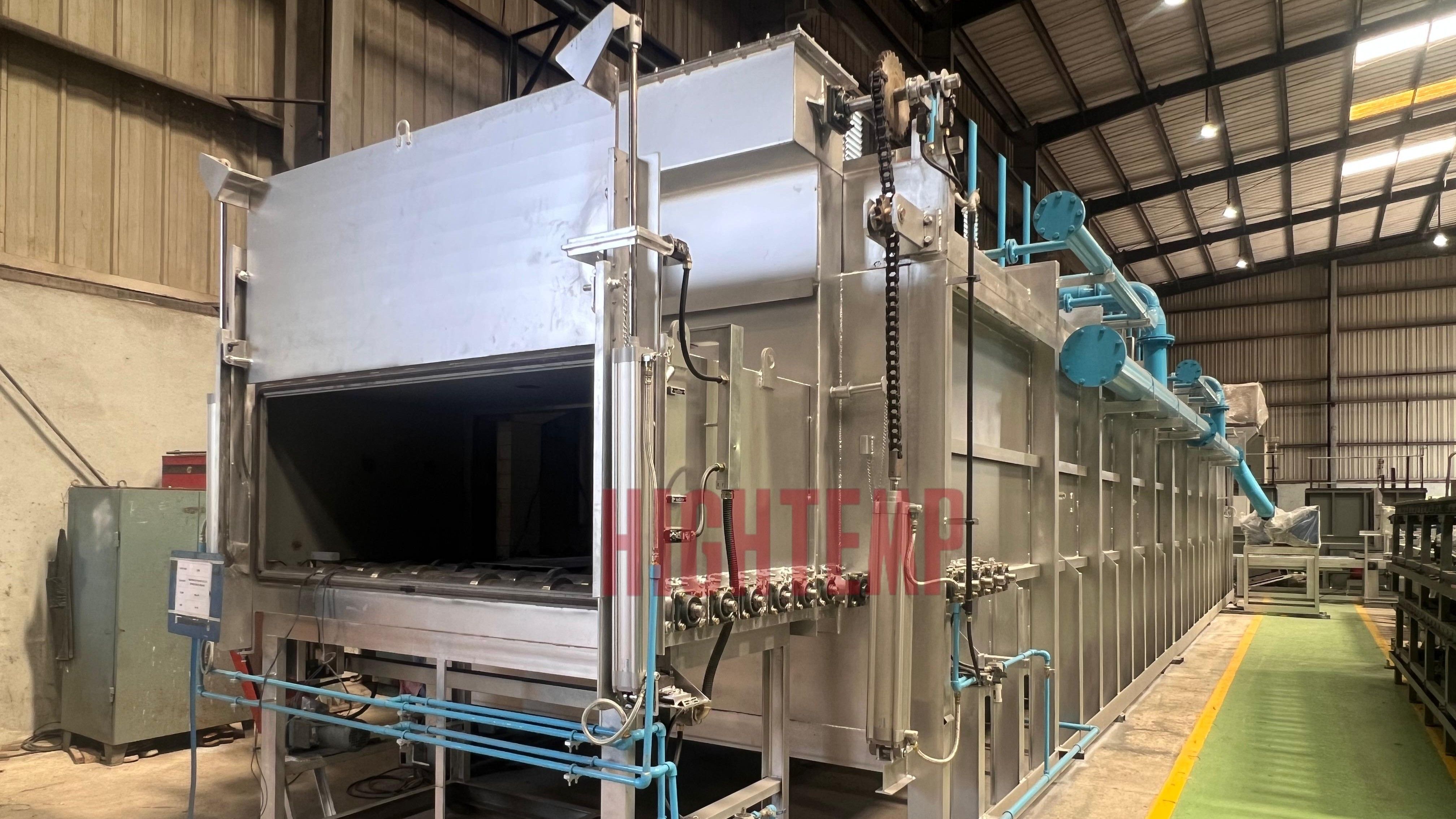

At HIGHTEMP, our Isothermal Annealing Furnaces are engineered to process materials such as carbon steels (e.g., AISI 1040, 1050), alloy steels (e.g., 4140, 4340), cast iron (e.g., grey and ductile iron), and stainless steels (e.g., 304, 316) by heating them to temperatures between 700°C and 900°C, holding them at an isothermal phase to achieve uniform microstructures, and cooling them in a controlled manner. This process reduces hardness, enhances machinability, and improves mechanical properties for components such as gears, shafts, bearings, and engine blocks, meeting the high standards of the automotive, aerospace, and manufacturing industries.