- The mesh belt conveyor ensures consistent heat exposure for all components, improving quality.
- Advanced design reduces wear and frequent maintenance.
- Easily integrated into continuous production lines, allowing flexibility for small to large-scale operations.
- Optimized energy use and low emissions contribute to a more sustainable and eco-friendly production process.
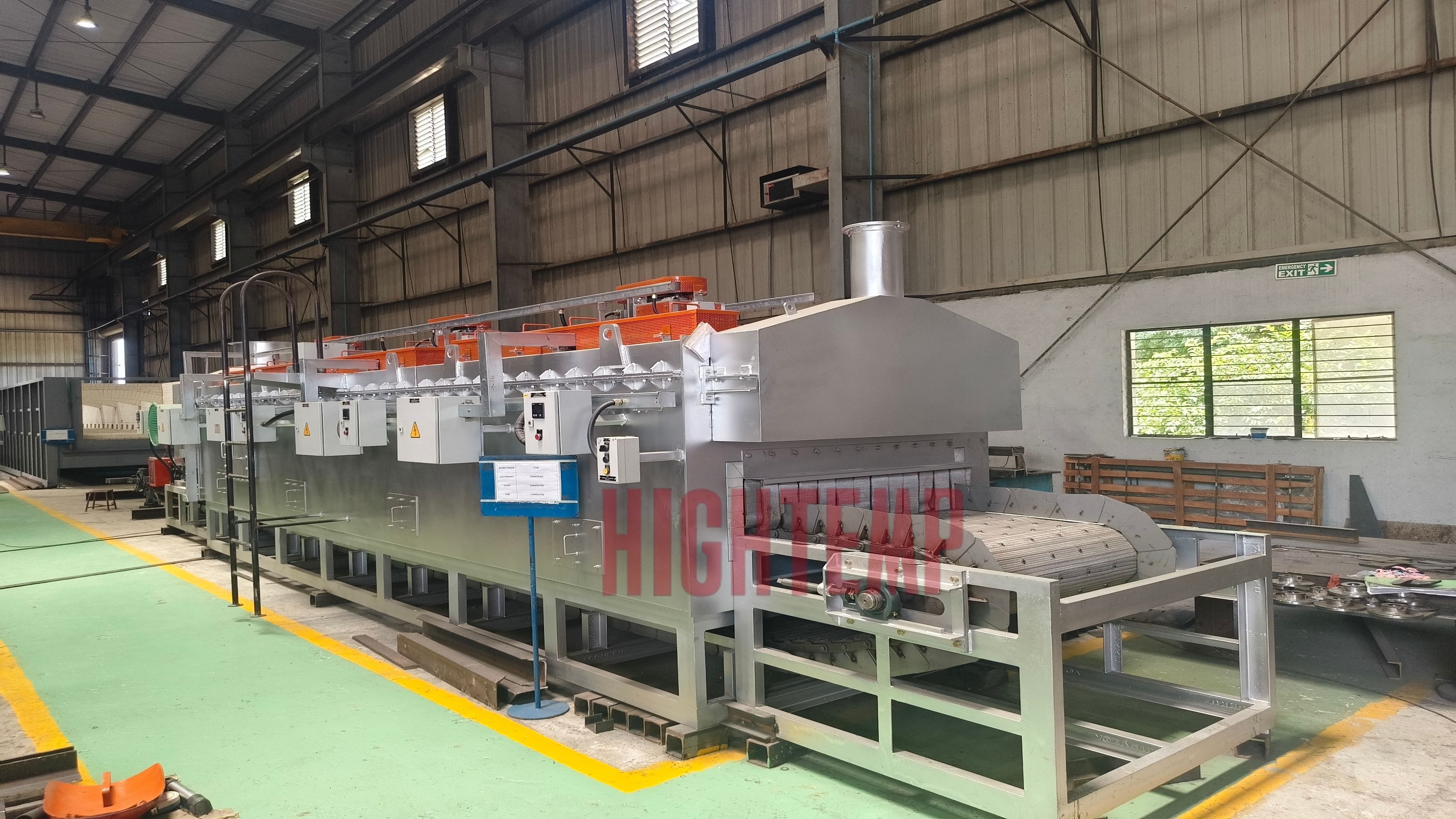

The Continuous Isothermal Annealing Furnace from HIGHTEMP is a highly efficient and precise heat treatment system designed for continuous annealing and processing of metal components, offering a controlled environment that ensures uniform heating, isothermal holding at the ideal temperature, and gradual cooling to enhance stress relief, ductility, machinability, and overall material performance, with key components including a high-quality mesh or roller belt for smooth transportation, multiple heating zones for consistent temperature control, isothermal holding zones to maintain the ideal temperature, a cooling zone to prevent distortion, and an advanced control system integrated with SCADA for real-time monitoring of temperature, atmosphere, and conveyor speed, making it suitable for a wide range of materials such as low-carbon, medium-carbon, alloy, high-carbon steels, and stainless steels, and ideal for processing components like gears, shafts, springs, valves, bearings, and crankshafts in industries such as automotive, aerospace, machinery, and manufacturing.
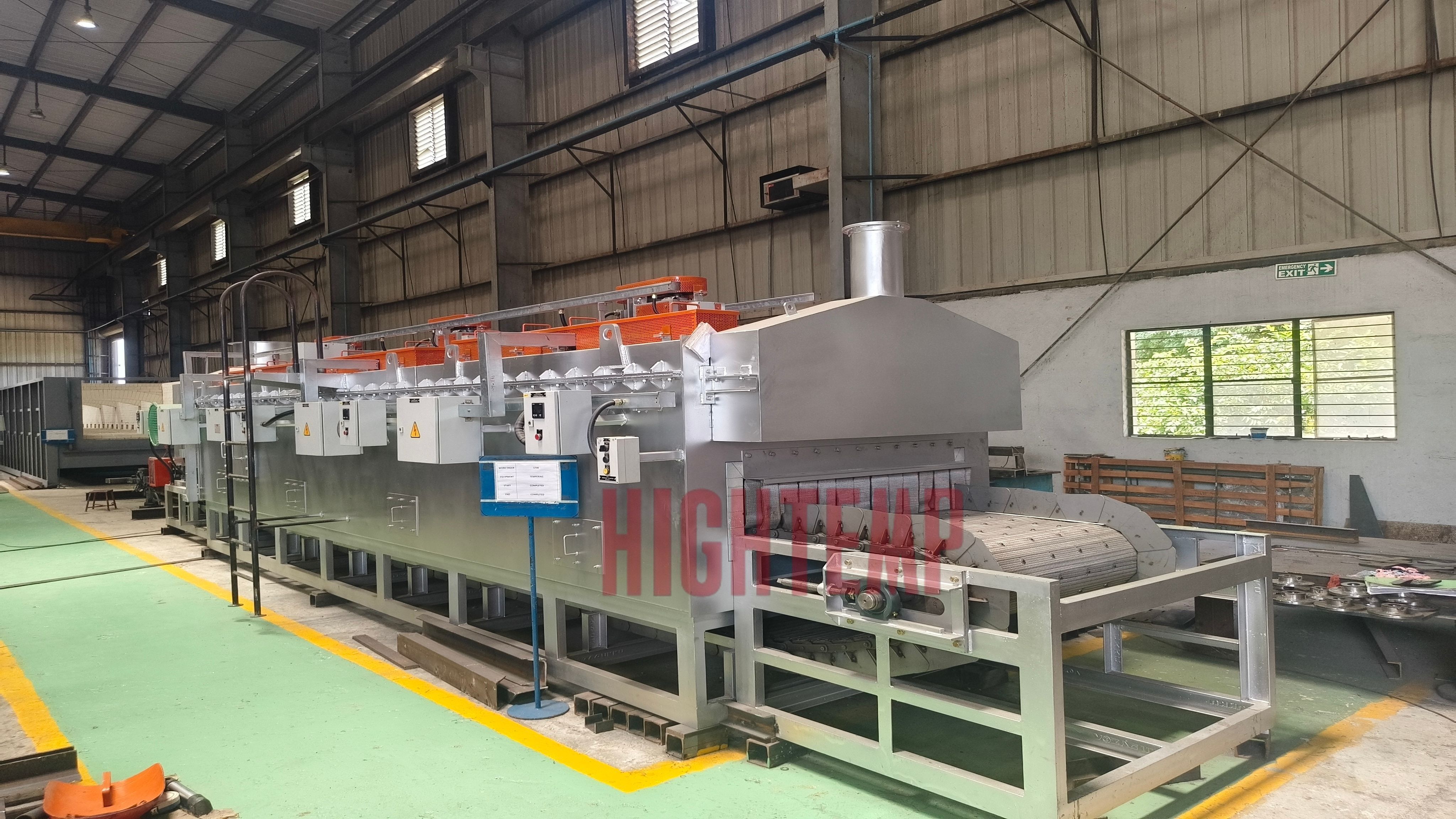

HIGHTEMP's Continuous Normalising Furnace is an advanced heat treatment solution designed to improve the mechanical properties of steel components by refining grain structure, enhancing toughness, and relieving internal stresses. It operates continuously, providing high throughput while maintaining uniform temperature distribution throughout the process. The furnace offers flexibility with electric or gas-fired heating options and features a state-of-the-art control system for precise temperature and atmosphere regulation. Suitable for treating materials like low-carbon, medium-carbon, and alloy steels, the Continuous Normalising Furnace is ideal for processing components such as gears, shafts, crankshafts, and valve components. The system ensures consistent and high-quality results with minimal distortion, contributing to enhanced hardness, toughness, and machinability of the treated parts. With its energy-efficient design and high productivity, HIGHTEMP’s Continuous Normalising Furnace is a reliable and cost-effective solution for industries such as automotive, aerospace, and manufacturing.
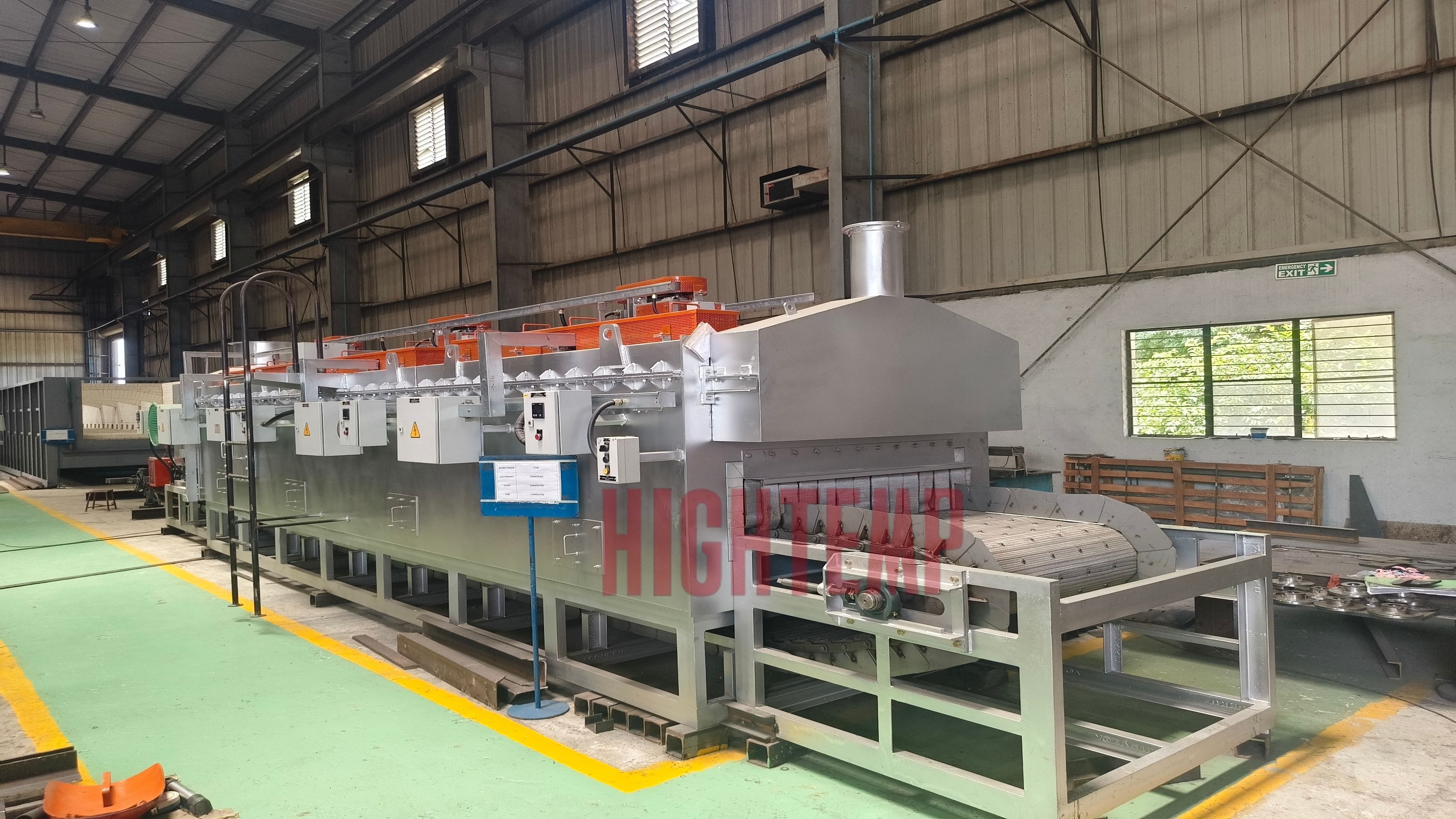

The Continuous Mesh Belt Hardening Furnace from HIGHTEMP is a highly efficient and versatile heat treatment solution designed for the continuous processing of steel components, featuring a durable mesh belt for smooth transportation, multiple heating zones for precise temperature control, a quenching station for rapid cooling to achieve superior hardness and wear resistance, an advanced control system for real-time monitoring and regulation of key parameters such as temperature, atmosphere, and conveyor speed, and the ability to process a wide range of materials including low-carbon steels, medium-carbon steels, alloy steels, high-carbon steels, and stainless steels, making it ideal for high-volume production in industries such as automotive, aerospace, machinery, and tooling, where consistent quality, improved product performance, and energy efficiency are essential.