- The furnace ensures consistent and accurate temperature regulation throughout the entire annealing process, resulting in uniform material properties.
- The isothermal annealing process enhances the ductility, machinability, and overall performance of the material by relieving internal stresses and reducing brittleness.
- Continuous operation enables high-volume processing, increasing production efficiency and reducing lead times.
- The furnace is capable of processing a wide range of materials, including low-carbon, medium-carbon, alloy, high-carbon steels, and stainless steels, making it suitable for diverse applications.
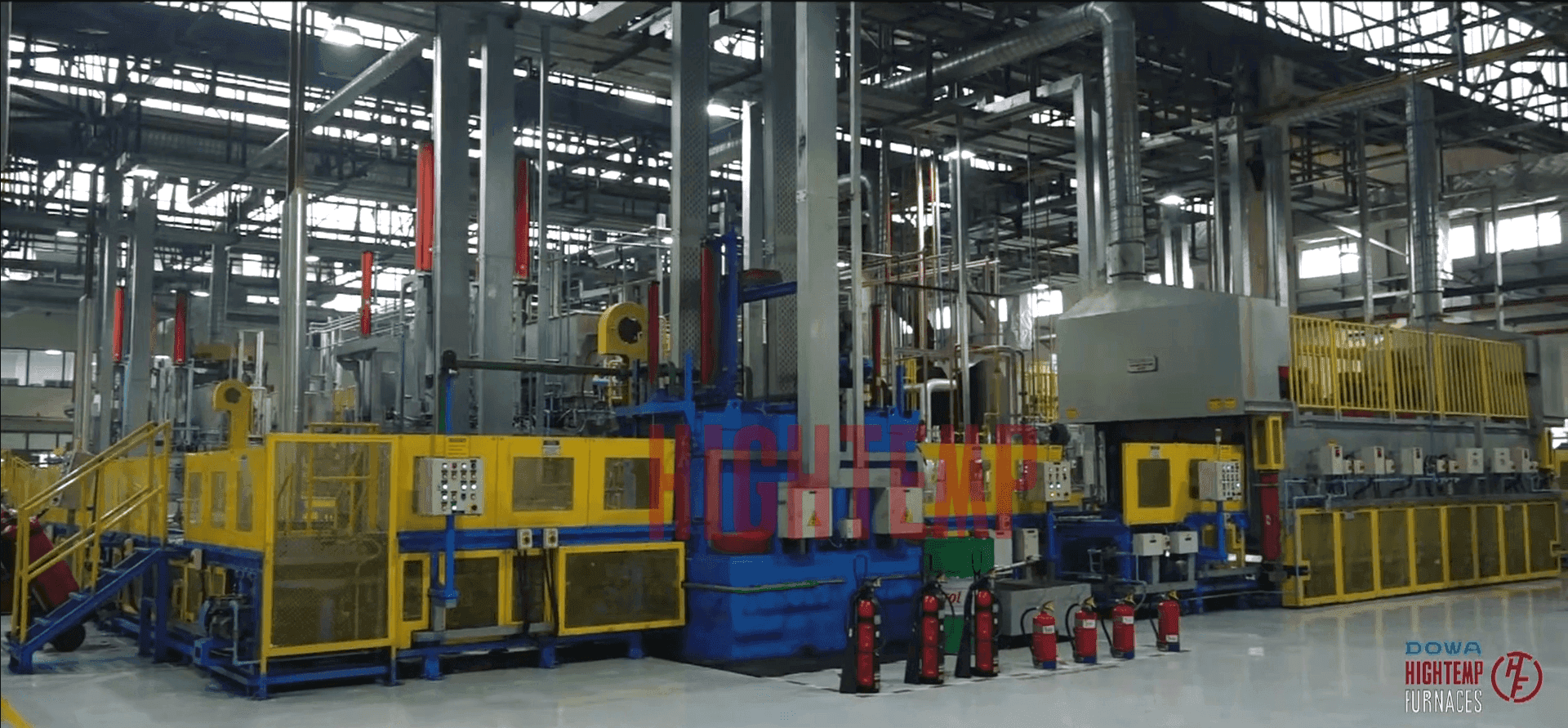

The HIGHTEMP Continuous Hardening and Tempering Furnace is a cutting-edge solution designed for high-volume heat treatment applications. Engineered to deliver precision, efficiency, and reliability, this furnace seamlessly integrates the hardening and tempering processes, meeting the demands of industries where consistent quality and performance are crucial. With a temperature range of 850°C to 1,100°C for hardening, the furnace ensures precise austenitization to achieve maximum hardness. For tempering, it operates between 150°C and 650°C, effectively relieving stresses and reducing brittleness to enhance toughness while maintaining strength.
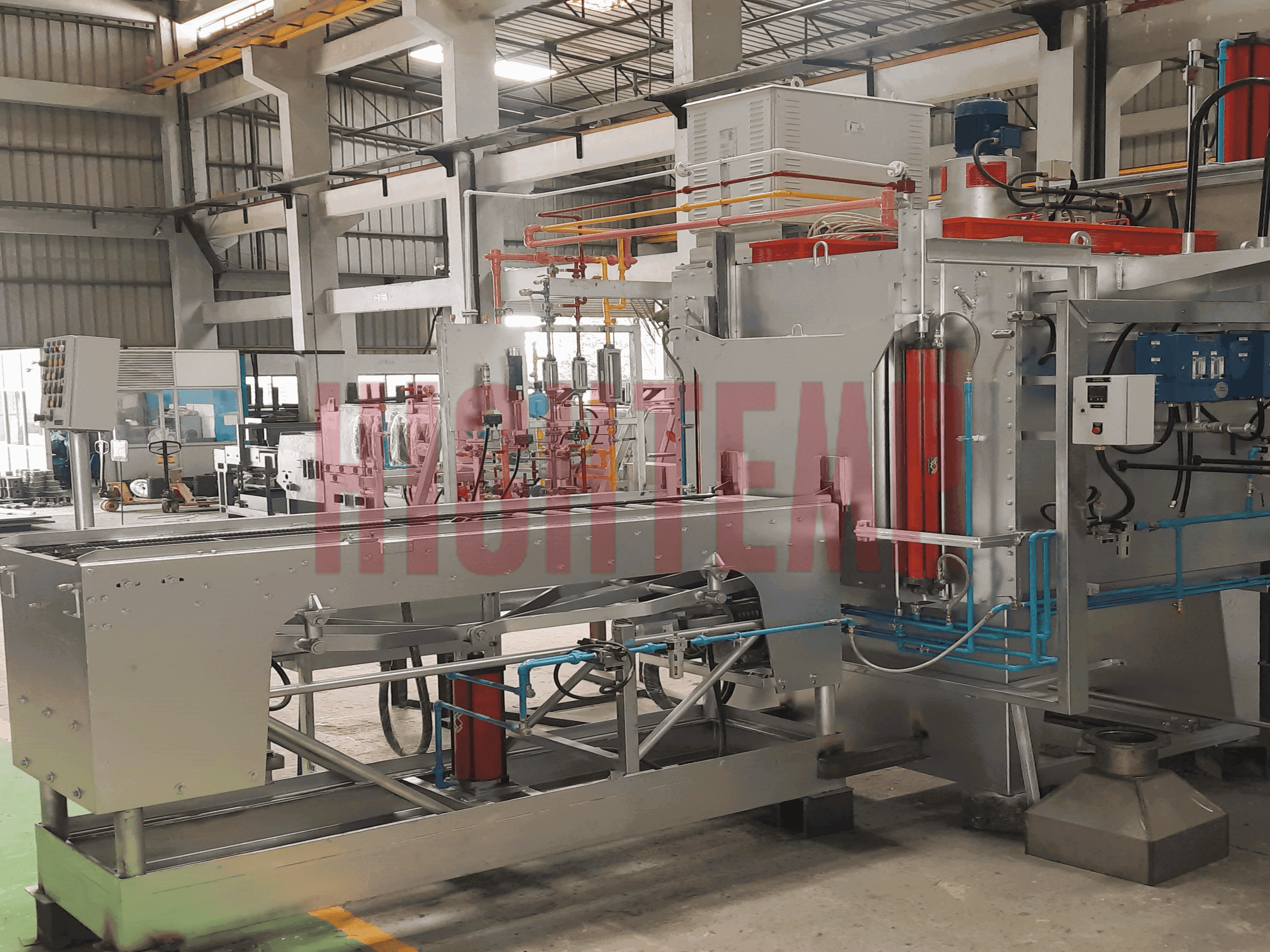

Our Sealed Quench Furnace is ideal for the heat treatment of components like gears, shafts, crankshafts, pins, bolts, fasteners, and tool & die parts. It offers a controlled environment for carburising processes, which are critical for enhancing the mechanical properties of materials such as EN8, EN9, EN19, EN24, 16MnCr5, 20MnCr5, SAE 8620, and EN31. Carburising is used to add carbon to the surface of low-carbon steels to enhance their hardness and wear resistance, while keeping the core material tough and ductile. After carburising, tempering is performed to reduce brittleness and improve the toughness of the hardened surface. It also helps relieve internal stresses that may result from the quenching process. This furnace can perform other heat treatment processes, including hardening, carbonitriding, normalizing, nitrocarburizing, nitriding, austempering, neutral hardening, annealing, and bright hardening.
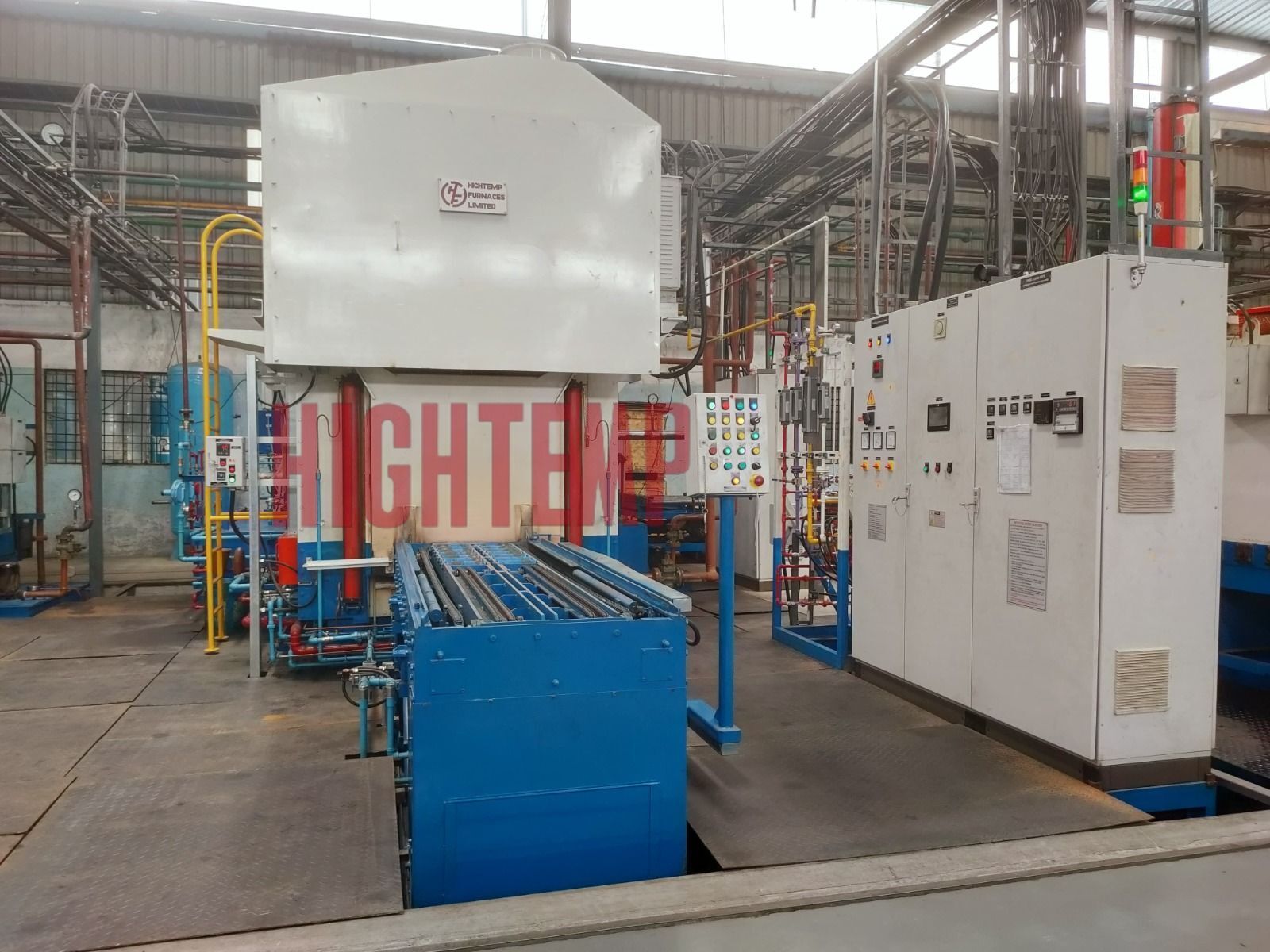

The Sealed Quench Furnace is a high-performance heat treatment system designed for austempering, carburising, and tempering. Ideal for components like gears, shafts, clutch plates, springs, fasteners, and crankshafts, it delivers superior wear resistance, toughness, and fatigue strength. Austempering is a specialized process that transforms steel into an ausferrite microstructure, enhancing toughness, wear resistance, and fatigue strength with minimal distortion. This makes it ideal for components that require superior mechanical performance. This furnace can perform other heat treatment processes, including hardening, carbonitriding, normalizing, nitrocarburizing, nitriding, neutral hardening, annealing, and bright hardening.