- Equipped with modern automation and control systems, allowing for consistent results with minimal operator intervention.
- Ensures superior finish quality and mechanical integrity, crucial for components requiring tight tolerances.
- Capable of treating smaller batches or large volumes, Vacuum Chamber Furnaces offer flexibility to meet the demands of both low and high-volume production.
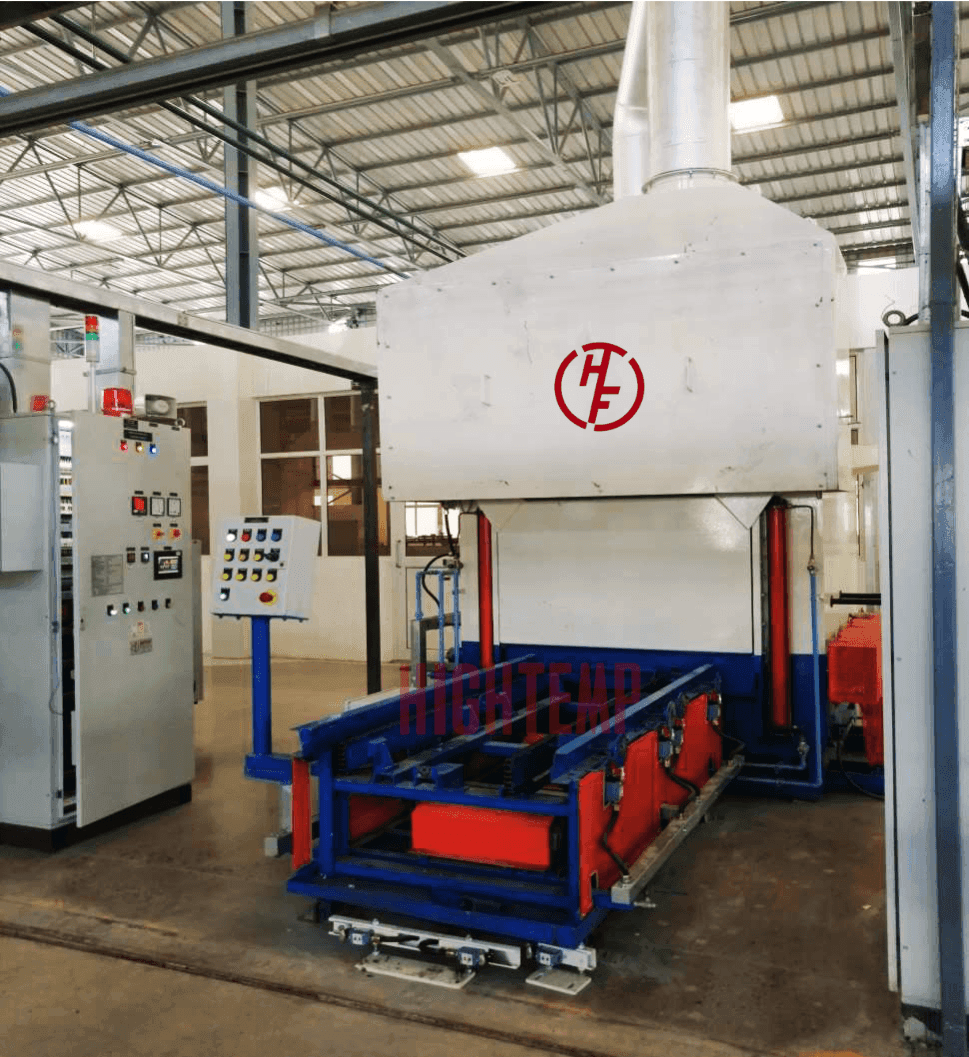

HIGHTEMPs Tempering Furnaces is a Chamber Furnace designed for operating at temperatures ranging from 100°C to 650°C to achieve desired mechanical properties. It also features production capacities ranging from 200 kg to 2500 kg gross per batch. The heating and circulation system ensures uniform heat distribution, for every steel parts in industries such as automotive, aerospace, and manufacturing, ensuring precise temperature control, energy efficiency, and reliable performance.
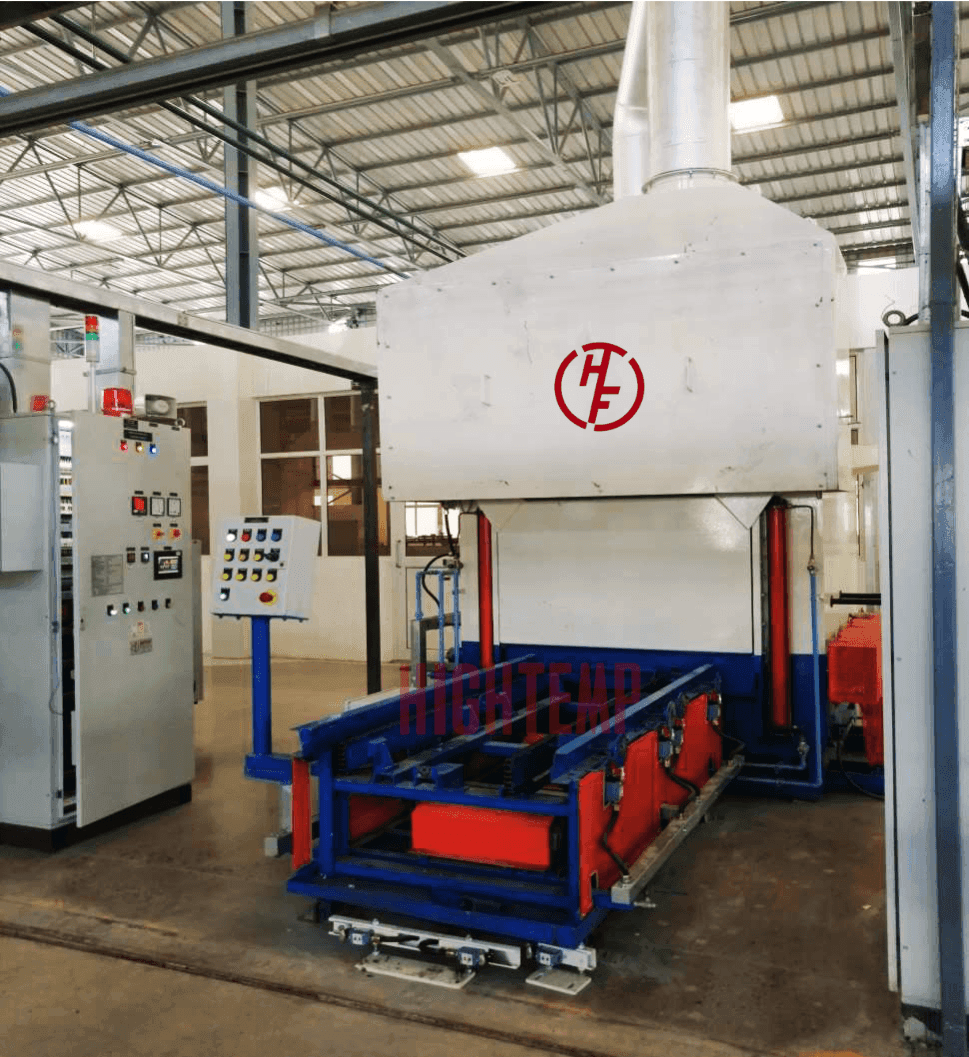

Our Atmospheric Chamber Furnaces are advanced industrial furnaces designed to maintain a controlled atmosphere, safeguarding materials from oxidation and other harmful reactions during heat treatment processes. Widely used across industries such as automotive, aerospace, and manufacturing, these furnaces are ideal for applications like carburising, carbonitriding, annealing, and other thermal treatments. By utilizing inert gases like nitrogen, nitrogen-methanol or argon, or Endogas mixture, our furnaces offer precise control over the materials microstructure and properties, ensuring optimal results for every application.
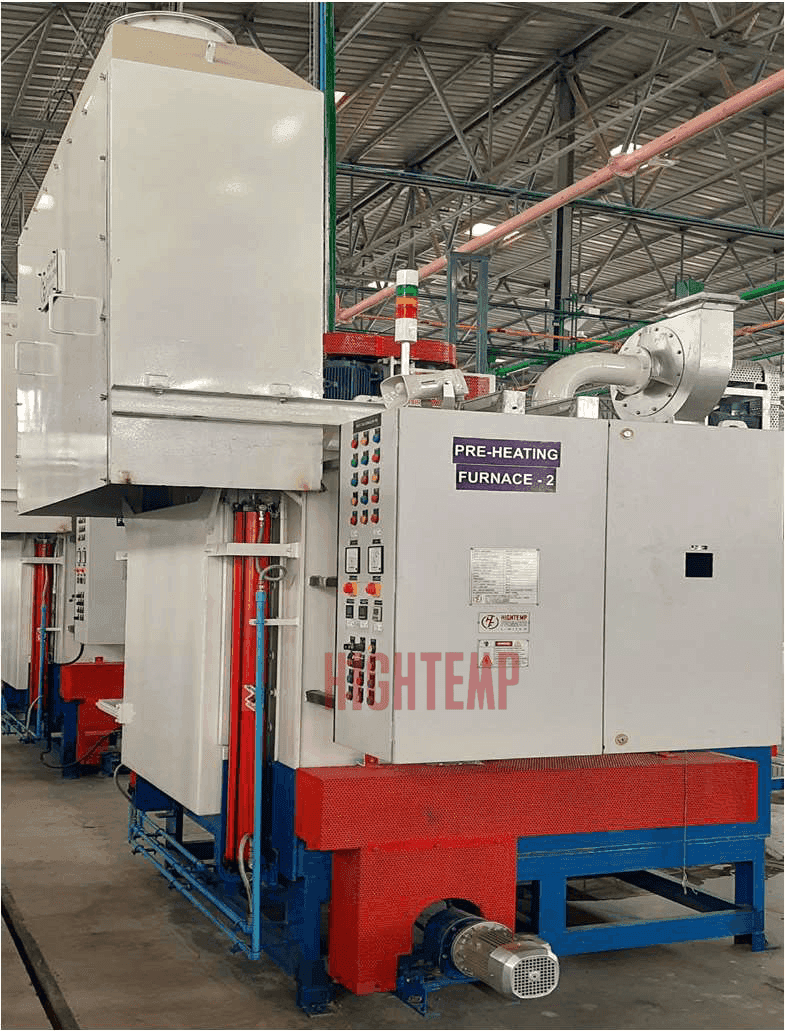

Our Blueing Furnaces are designed to provide a protective, corrosion-resistant oxide layer on steel components by heating them to temperatures between 250°C to 350°C in a controlled atmosphere, followed by a chemical treatment to create a uniform, visually appealing finish, making them ideal for enhancing the durability and aesthetic appeal of components in industries such as automotive (brake components, gears, exhaust parts), aerospace (fasteners, bolts, shafts), and general manufacturing (tools, machine parts), with materials ranging from carbon steels to alloy steels and stainless steels, all while offering excellent corrosion resistance, increased wear resistance, and a consistent, high-quality finish for large-scale production.