- The blue oxide layer significantly enhances the component’s resistance to rust and corrosion, extending its lifespan.
- Perfect for large-scale production with automated systems ensuring uniform treatment across large batches.
- Ensures a consistent, smooth, and visually appealing blue-black finish across all parts, regardless of size.
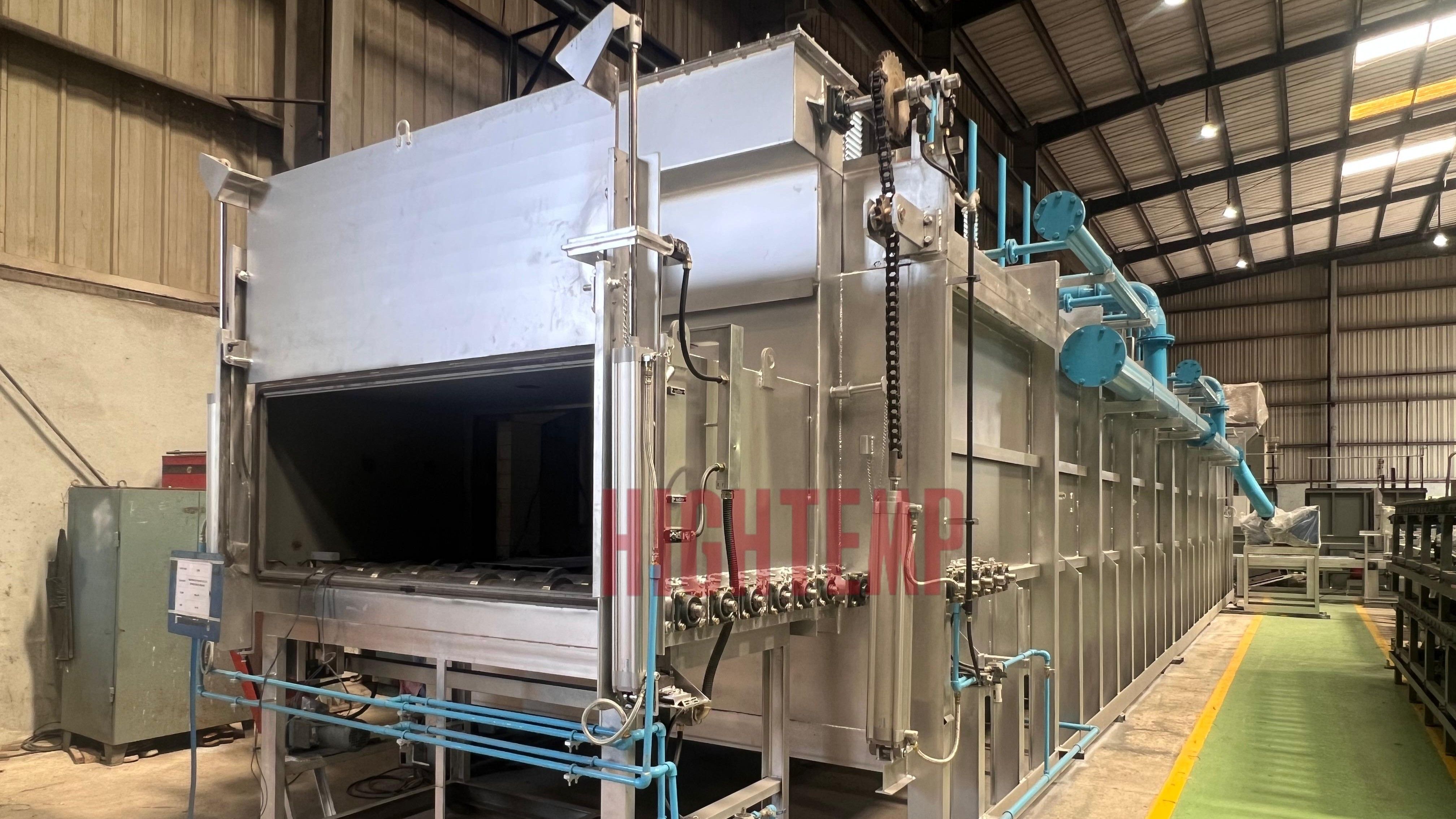

Our Decarb Annealing Furnaces are designed to process steel components by heating them to temperatures ranging from 800°C to 950°C in a controlled neutral or reducing atmosphere, promoting the removal of excess carbon from the surface to improve the material's surface quality and prepare it for further processes such as plating, welding, and machining, making it ideal for applications in industries like automotive, aerospace, and manufacturing for components such as exhaust valves, shafts, and gears, where surface integrity and uniform material properties are crucial for performance and durability.
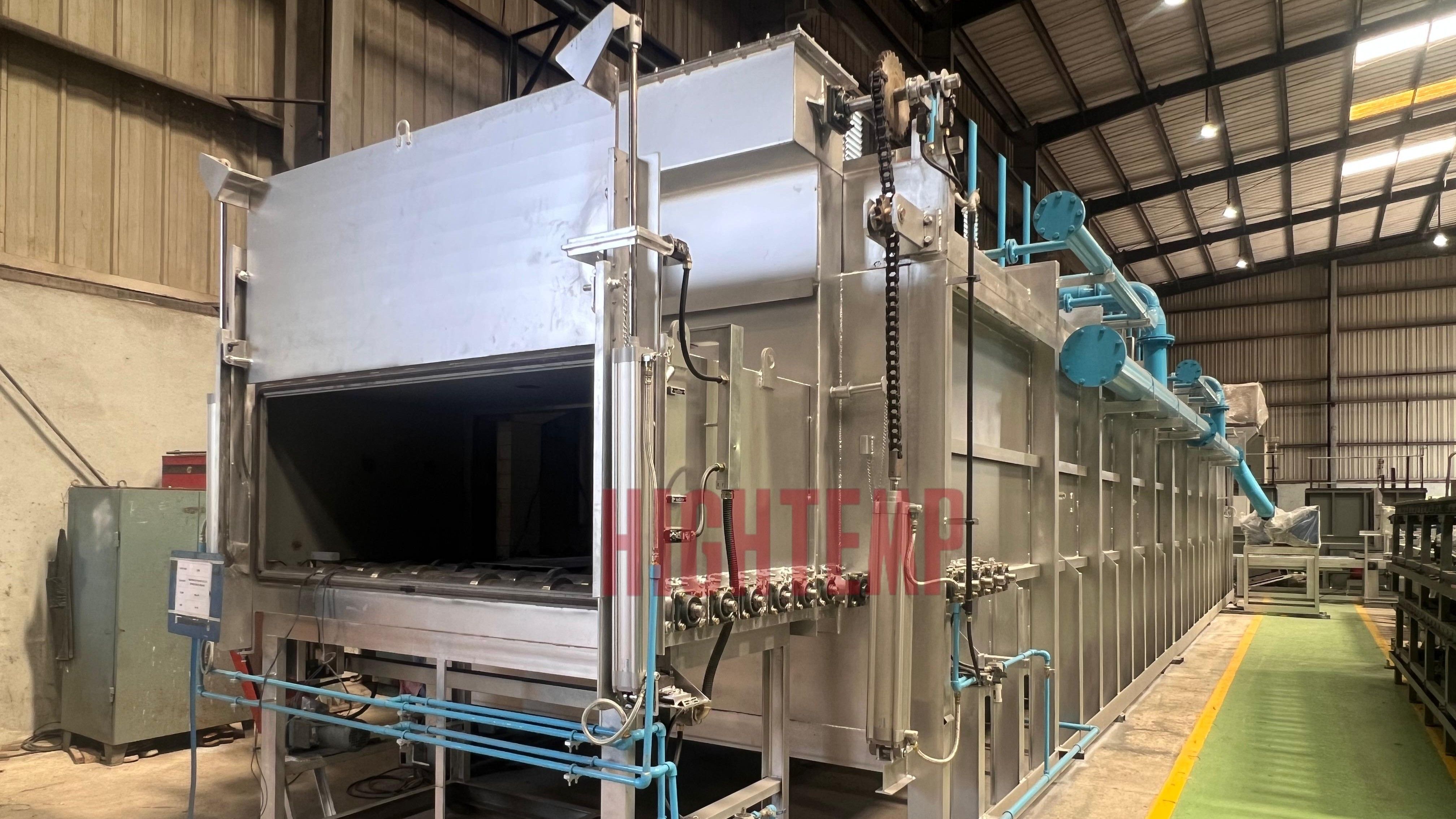

At HIGHTEMP, our Isothermal Annealing Furnaces are engineered to process materials such as carbon steels (e.g., AISI 1040, 1050), alloy steels (e.g., 4140, 4340), cast iron (e.g., grey and ductile iron), and stainless steels (e.g., 304, 316) by heating them to temperatures between 700°C and 900°C, holding them at an isothermal phase to achieve uniform microstructures, and cooling them in a controlled manner. This process reduces hardness, enhances machinability, and improves mechanical properties for components such as gears, shafts, bearings, and engine blocks, meeting the high standards of the automotive, aerospace, and manufacturing industries.
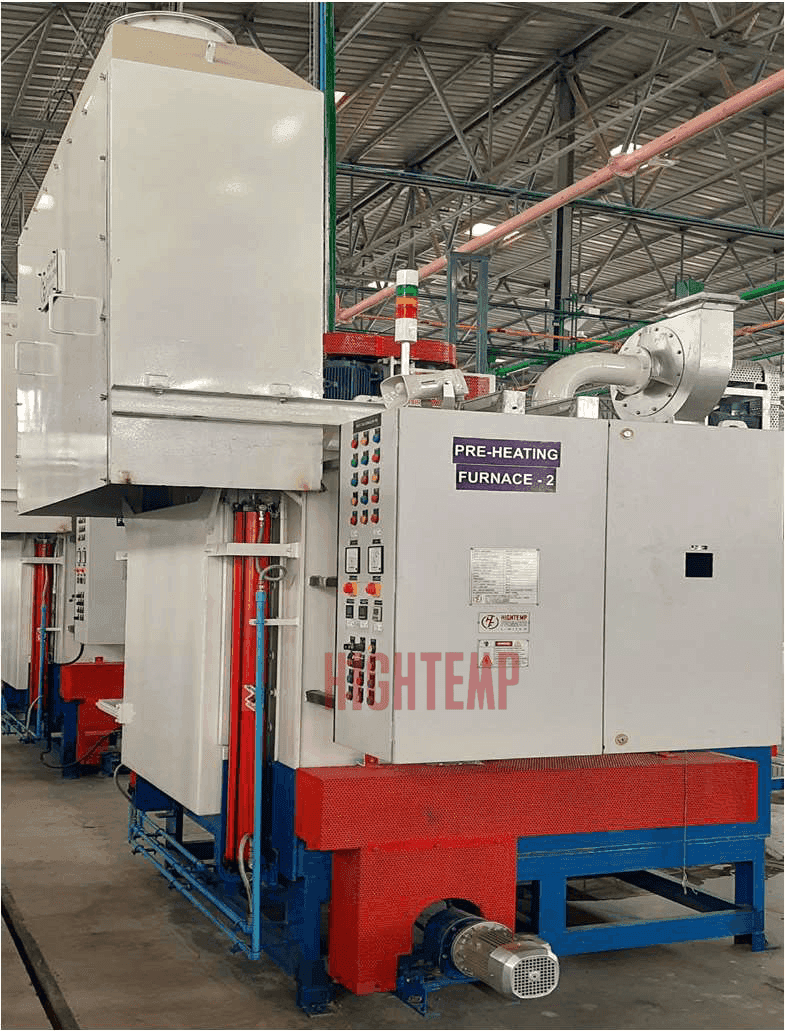

HIGHTEMP Decarb Annealing Furnaces operate in a controlled atmosphere (800°C to 950°C) using gases like hydrogen or carbon monoxide to reduce surface carbon, enhancing weldability, surface quality, and machinability. Ideal for automotive, aerospace, and manufacturing applications, these furnaces process components like exhaust valves, shafts, and gears before plating, coating, or welding, minimizing oxidation and scaling. With production rates ranging from 1 ton/day to 6 tons/day for batch-type and 500kg/hr to 2000kg/hr for continuous-type furnaces, we offer flexible solutions for various production needs.