- The controlled atmosphere prevents oxidation, ensuring a clean, smooth surface on materials during heat treatment.
- Ensures uniform heating and treatment, reducing defects like scaling, pitting, or surface imperfections.
- Accelerates heat treatment cycles by maintaining the optimal atmosphere, improving overall production speed.
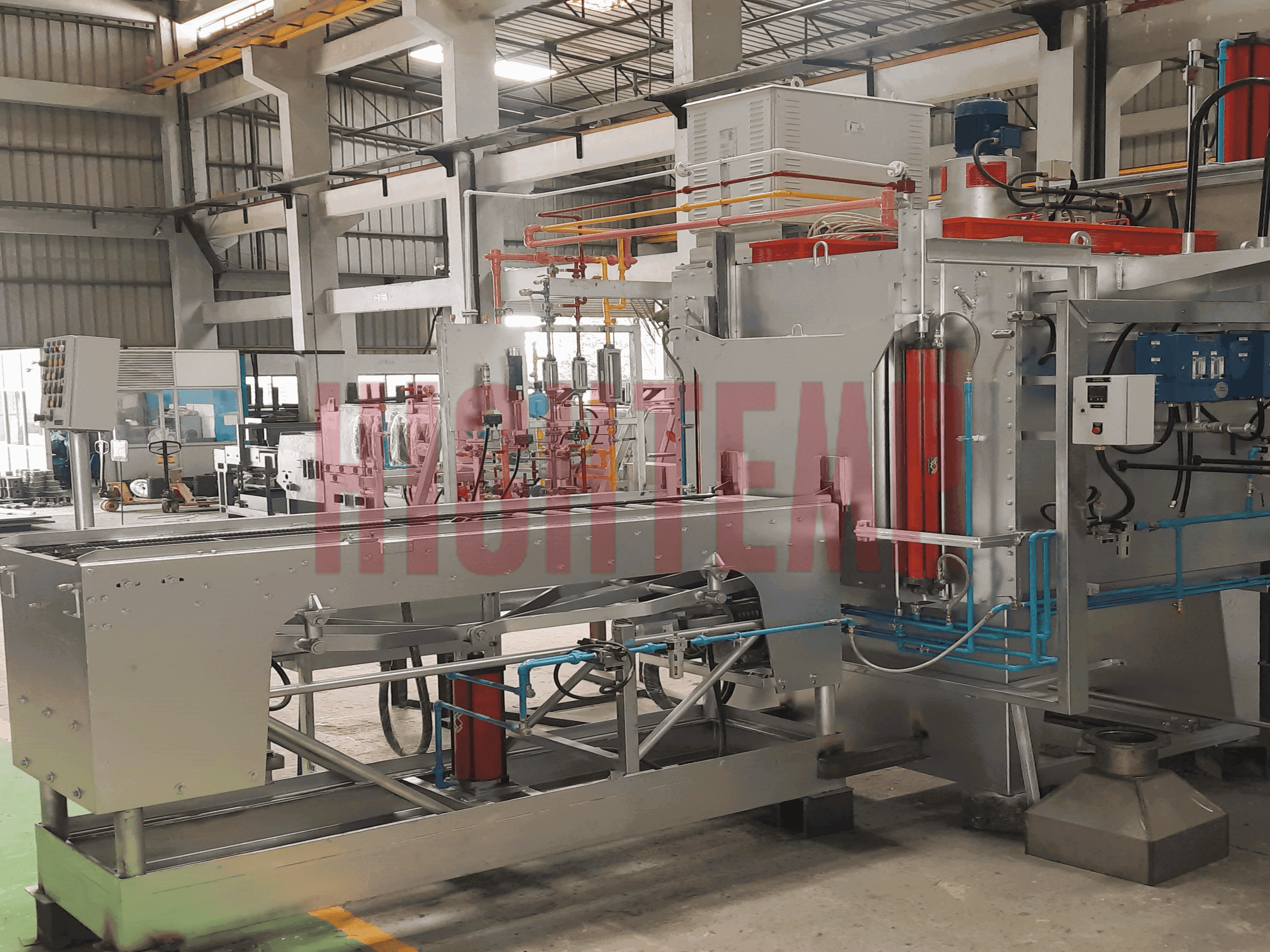

Our Sealed Quench Furnace is ideal for the heat treatment of components like gears, shafts, crankshafts, pins, bolts, fasteners, and tool & die parts. It offers a controlled environment for carburising processes, which are critical for enhancing the mechanical properties of materials such as EN8, EN9, EN19, EN24, 16MnCr5, 20MnCr5, SAE 8620, and EN31. Carburising is used to add carbon to the surface of low-carbon steels to enhance their hardness and wear resistance, while keeping the core material tough and ductile. After carburising, tempering is performed to reduce brittleness and improve the toughness of the hardened surface. It also helps relieve internal stresses that may result from the quenching process. This furnace can perform other heat treatment processes, including hardening, carbonitriding, normalizing, nitrocarburizing, nitriding, austempering, neutral hardening, annealing, and bright hardening.
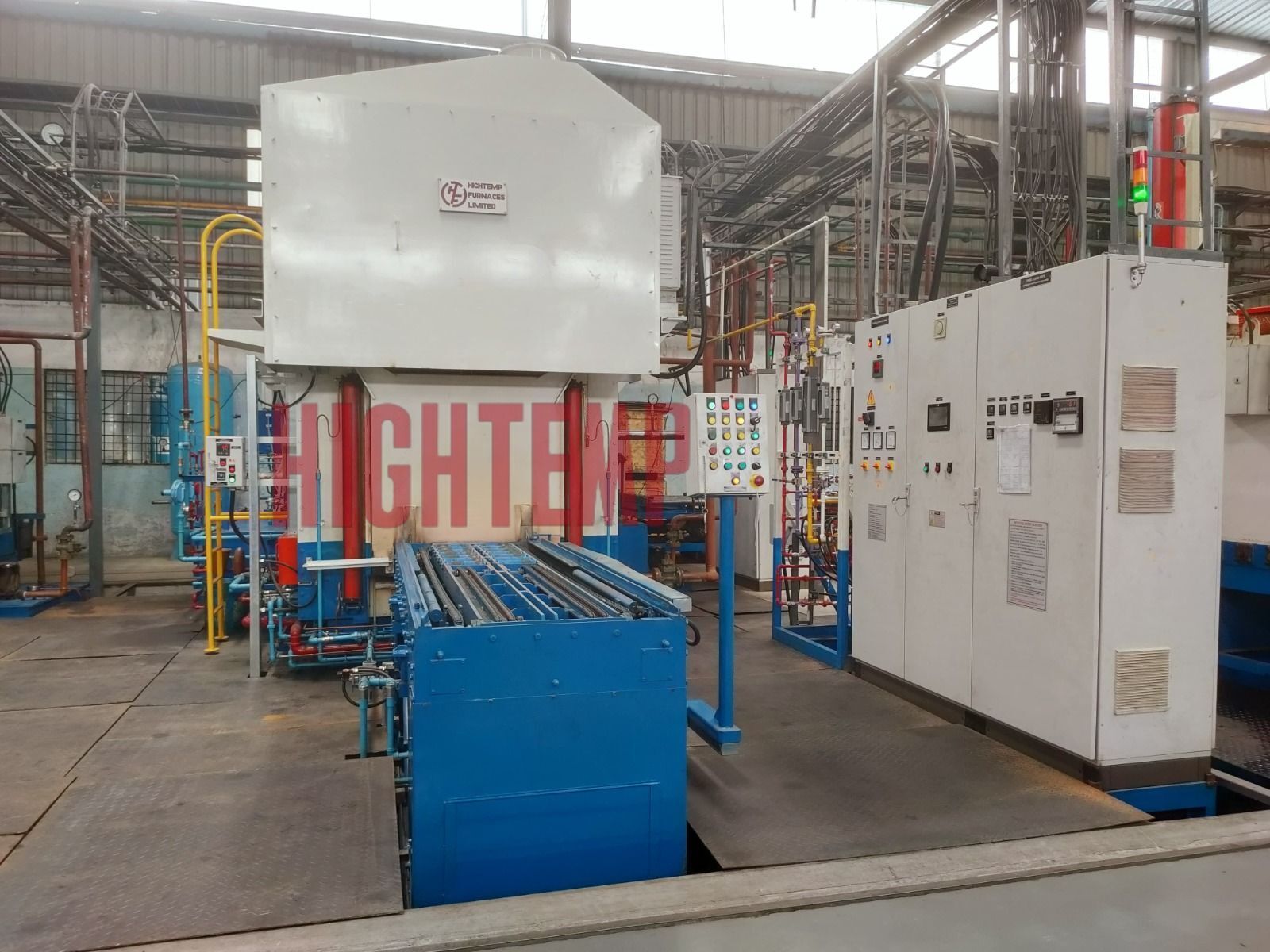

The Sealed Quench Furnace is a high-performance heat treatment system designed for austempering, carburising, and tempering. Ideal for components like gears, shafts, clutch plates, springs, fasteners, and crankshafts, it delivers superior wear resistance, toughness, and fatigue strength. Austempering is a specialized process that transforms steel into an ausferrite microstructure, enhancing toughness, wear resistance, and fatigue strength with minimal distortion. This makes it ideal for components that require superior mechanical performance. This furnace can perform other heat treatment processes, including hardening, carbonitriding, normalizing, nitrocarburizing, nitriding, neutral hardening, annealing, and bright hardening.
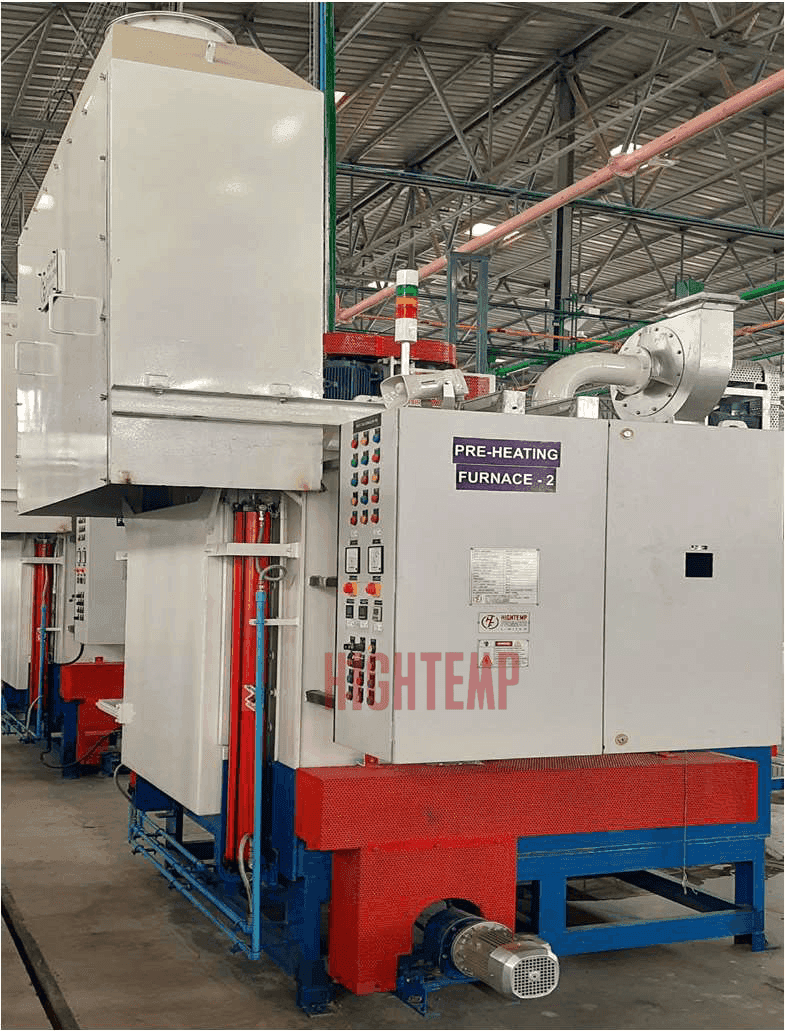

HIGHTEMP Decarb Annealing Furnaces operate in a controlled atmosphere (800°C to 950°C) using gases like hydrogen or carbon monoxide to reduce surface carbon, enhancing weldability, surface quality, and machinability. Ideal for automotive, aerospace, and manufacturing applications, these furnaces process components like exhaust valves, shafts, and gears before plating, coating, or welding, minimizing oxidation and scaling. With production rates ranging from 1 ton/day to 6 tons/day for batch-type and 500kg/hr to 2000kg/hr for continuous-type furnaces, we offer flexible solutions for various production needs.